How small can a CNC machine cut?
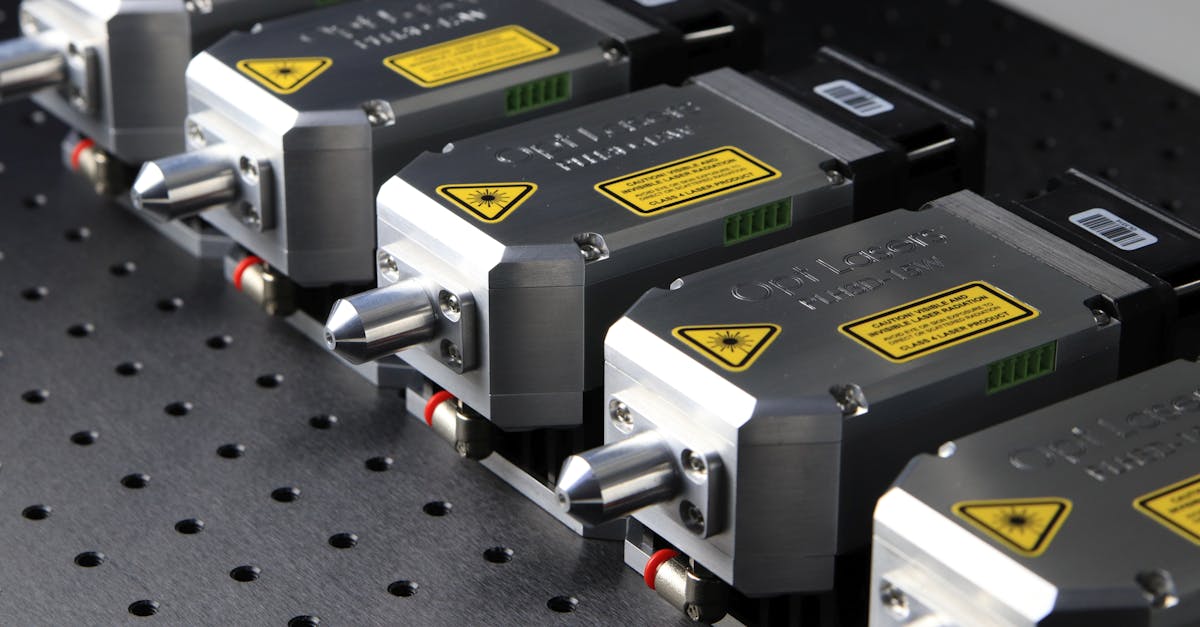
Table Of Contents
Achieving SubMicron Levels of Accuracy
To achieve sub-micron levels of accuracy in CNC machining, precision is key. This level of precision requires meticulous attention to detail in every aspect of the machining process. From the selection of the cutting tools to the programming of the machine, each step must be carefully calibrated to ensure that the desired level of accuracy is achieved.
In addition to precision, achieving sub-micron levels of accuracy also requires the use of advanced measuring and feedback systems. These systems provide real-time data on the performance of the machine, allowing for adjustments to be made on the fly to maintain the desired level of accuracy. By combining precision machining techniques with advanced measurement and feedback systems, CNC machines can achieve sub-micron levels of accuracy, opening up a wide range of new possibilities in industries where ultra-high precision is required.
Precision Machining Techniques
Precision machining techniques play a key role in achieving high levels of accuracy in CNC cutting processes. One of the fundamental techniques used is the utilization of high-quality cutting tools and materials. The selection of the appropriate tools and materials is crucial in ensuring that the cuts are precise and consistent throughout the process. Additionally, maintaining the tools in optimal condition, with regular sharpening and replacement as needed, is essential for achieving the desired level of precision.
In addition to tool selection, another important precision machining technique is the optimization of cutting parameters such as speed, feed rate, and depth of cut. By fine-tuning these parameters to the specific requirements of the material being cut, manufacturers can minimize errors and achieve sub-micron levels of accuracy in their CNC machining operations. Constant monitoring and adjustment of these parameters during the cutting process are necessary to ensure that the final product meets the desired specifications.
Common Challenges in Achieving UltraSmall Cuts
Achieving ultra-small cuts using CNC machines comes with its fair share of challenges. One of the key obstacles in attaining precision at such minuscule levels is the issue of tool deflection. When working with tiny tools on delicate materials, even the slightest displacement in the tool can lead to inaccurate cuts. This can be particularly problematic when trying to achieve sub-micron levels of precision, as any deviation from the intended cutting path can significantly impact the final result.
Another common challenge in ultra-small CNC cutting is the control of heat generation. As the tools used for these cuts are extremely small, they are more prone to overheating due to the increased friction during the cutting process. Heat can not only affect the tool life but can also cause thermal deformation in the workpiece, leading to dimensional inaccuracies. Proper cooling methods and efficient chip removal techniques are crucial in minimizing the heat buildup and ensuring consistent and precise cutting at the micro-level.
Minimizing Vibration
To minimize vibration in CNC machining processes, it is crucial to carefully control and adjust the cutting parameters. This involves optimizing factors such as spindle speed, feed rate, and depth of cut to ensure smoother cutting operations. By fine-tuning these settings, machinists can reduce the chances of vibration affecting the precision of the cuts.
In addition to optimizing cutting parameters, the use of high-quality cutting tools and tool holders can also help in minimizing vibration. Choosing tools that are specifically designed for stability and rigidity can significantly reduce the vibrations that occur during the machining process. Furthermore, ensuring that the tool holders are properly balanced and securely mounted can further enhance the stability of the cutting operation and improve the overall quality of the machined parts.
Advancements in Miniature CNC Cutting Technology
Advancements in miniature CNC cutting technology have revolutionized the precision machining industry by enabling the production of ultra-small cuts with remarkable accuracy. These advancements have made it possible to achieve cutting dimensions at the sub-micron level, pushing the boundaries of what was previously deemed achievable in manufacturing processes. With the integration of high-end CNC systems, cutting-edge tools, and advanced software algorithms, manufacturers can now create intricate and detailed components with unprecedented levels of precision.
One of the key drivers behind the advancements in miniature CNC cutting technology is the continual improvement in machine design and engineering. Manufacturers have focused on developing machines that offer improved rigidity, reduced thermal drift, and enhanced vibration damping properties. By minimizing these factors that can affect cutting accuracy, CNC machines can now deliver consistent and reliable performance even when cutting at ultra-small scales. These advancements have paved the way for new opportunities in industries such as aerospace, electronics, and medical devices where precision and miniature components are in high demand.
Micro Machining Applications
Micro machining applications involve working with extremely small components and intricate designs. These applications are commonly found in industries such as electronics, aerospace, and medical devices, where precision and accuracy are of utmost importance. With the advancements in CNC technology, manufacturers can now achieve sub-micron levels of accuracy, allowing for the production of complex micro parts with tight tolerances.
One of the key benefits of micro machining is the ability to create miniaturized components that are essential for various high-tech devices. For example, in the electronics industry, micro machining is used to produce tiny sensors, connectors, and other critical parts that are integrated into smartphones, computers, and other electronic gadgets. Additionally, in the medical field, micro machining is utilized to fabricate miniature surgical instruments, implants, and components for medical devices, enabling advancements in healthcare technologies.
FAQS
Can CNC machines achieve sub-micron levels of accuracy?
Yes, CNC machines can achieve sub-micron levels of accuracy through advanced precision machining techniques and technologies.
What are some common challenges in achieving ultra-small cuts with CNC machines?
Some common challenges include minimizing vibration, maintaining tool stability, and ensuring proper chip evacuation when cutting at extremely small scales.
How can vibration be minimized when cutting with a CNC machine at ultra-small scales?
Vibration can be minimized by using high-quality cutting tools, reducing cutting forces, optimizing cutting parameters, and ensuring the machine is properly calibrated and maintained.
What advancements have been made in miniature CNC cutting technology?
Advancements in miniature CNC cutting technology include the development of high-precision micro tools, improved machine rigidity and stability, and enhanced software algorithms for better tool path optimization.
What are some common applications of micro machining with CNC machines?
Micro machining with CNC machines is commonly used in industries such as electronics, medical devices, aerospace, and automotive for producing intricate and precise components at a microscopic scale.