Precision CNC Machining Services Are In Demand!
Key Takeaways
- Discover insights into Precision CNC Machining Services.
- Gain knowledge about the CNC Machine and its operation.
- Explore the capabilities of machining and its precision applications.
- Focus on the application of precision machining in Hybrid Vehicle Battery Packs.
- Delve into the EDMing of Carbides and the Grinding Process.
- Learn about Aerospace Applications and a CNC Lathe Machining Parts Company.
- Understand the significance of different materials like Carbon, Stainless Steel, and more.
- Realize the importance of Prototypes in CNC Machining Services.
- Examine Precision Metal Components and their adherence to Surface Design Guides.
- Get an overview of Passivation Powder Coat and its principles.
- Learn about other essential techniques like Spot Welding Electrodes and Type III Milling.
An Exploration of Precision CNC Machining Services
Precision CNC machining services play a crucial role in various industries worldwide, from producing intricate catheter components to machining precise metal pieces for landing gear parts. The ability to work with a wide range of materials such as brass, copper, titanium, and even stainless steel and carbon underscores the versatility and importance of precision machining services. With advancements in CAD/CAM systems and CNC threads, companies like Parsons have expanded their infrastructure to offer a variety of services including CNC milling, turning, and wire EDM. These services cater to the diverse needs of different sectors, demonstrating the value and stability that precision machining brings to the manufacturing process. Through a combination of state-of-the-art machinery and skilled applications engineers, the sector has witnessed an influx of techniques and modifications that enhance part features and overall product quality. The trade-off between quantities and tolerances, as well as the selection of suitable materials, play a critical role in maintaining the integrity and thermal conductivity of workpieces. As the industry continues to evolve, the importance of precision CNC machining services cannot be overstated, especially in meeting the demanding requirements of today's market.
Types of Precision CNC Machining Services
Precision CNC machining services encompass a wide range of capabilities to meet various industrial needs. These services involve intricate tasks such as polygon machining, CNC milling services, and deburring techniques. Companies offering precision CNC machining services cater to different sectors, including aerospace, automotive, and engineering. From machining intricate carvings to producing high-volume production runs, these services play a vital role in the manufacturing industry. The ability to work with diverse materials like alloys, engineering plastics, and sheet metal makes precision CNC machining services indispensable for creating precision components with tight tolerances and exceptional surface finishes.
Precision CNC machining services have seen a significant evolution due to advancements like additive manufacturing and CNC manufacturing equipment. Companies have also incorporated 3D printing services to enhance their capabilities and offer a wider range of solutions to their clients. The trend towards cost-effective and efficient machining processes has pushed companies to invest in CNC lathe machines and 5-axis milling machines. This growth in CNC machining capacities has enabled manufacturers to handle complex projects with ease and precision. The role of precision CNC machining services in producing components with precise dimensions, mating parts, and excellent surface finishes cannot be overstated.
Importance of Precision CNC Machining Services
Precision CNC machining services play a pivotal role across industries, from aerospace to automotive, ensuring intricate components are manufactured with utmost accuracy. In CNC machine shops in Antigua and Mozambique, leaders in aviation precision manufacturing rely on AS9100D and ISO 13485:2016 standards for quality assurance. Whether it's producing cap screws or threading considerations for manifolds, the impact of precision machining on engineering programs cannot be understated. With a diverse array of materials like Invar and Delrin at their disposal, these services cater to a vast footprint of applications, ranging from bone screws to automotive parts.
The importance of precision CNC machining services extends beyond mere manufacturing to the realm of IP rights and cookie-cutter solutions. Addressing the stringent requirements of industries like healthcare and automotive, CNC machining prototyping and multi-spindle screw machining have become synonymous with cutting-edge innovation. From titanium alloys in robotics to PTFE and HDPE in pipeline engineering, the depth and breadth of capabilities span multiple fields. With finishing options like powder coat and metal laser sintering, CNC machining ensures that even the most complex parts are crafted to perfection, adhering to strict tolerances and customer specifications.
Understanding the CNC Machine and its Mechanism
CNC machines are at the core of precision CNC machining services, driving the industry forward with their automated operations. Trend reports indicate a shift from manual to CNC operations due to factors like efficiency and repeatability. These machines function through a spindle turret, enabling precise tool actions like cutting threads and achieving parallelism. CNC metal machining encompasses a variety of materials, from copper and brass to plastics, with capabilities ranging from laser cutting to turning processes. Quality control is paramount, with factors like machine marks and measurement standards shaping the final product. Innovations in CNC technology ensure that manufacturing processes meet the highest standards, delivering precise components for a wide array of applications.

Basic Functionality of a CNC Machine
Efficiently operating a CNC machine is crucial for precision CNC machining services. Understanding the basic functionality involves the machine's ability to precisely cut materials like iron, expand_more, and steel based on the programmed commands. CNC machines use multiple axes to move the cutting tool in different directions simultaneously, enabling intricate part geometry to be achieved accurately. This precision ensures that parts meet customer specs consistently while also optimizing production schedules and part price. CNC machining types range from milling to turning to meet varied machining needs, from producing precision threads to creating screw holes or precise side cuts, catering to diverse industries from automotive to aerospace applications.
When it comes to ensuring the functionality of a CNC machine, attention to detail is paramount. Factors such as setup, spindle speed, and chip formation play a crucial role in the machining process. CNC machines are adept at machining various materials, from commodity aluminum to nickel coating, bronze, or even molybdenum, while maintaining tight tolerances in dimensions like diameter, flatness, and straightness properties. Understanding the machining surface, whether it's for OD grinding, lapping services, or ID grinding, is essential for achieving the desired part design events accurately. CNC machines are versatile, with the ability to handle intricate operations like heat expansion or resistance spot welding electrodes with precision, making them indispensable for a wide range of industries such as mold making services or injection molding for products like eyeglass frames or implants.
Types of CNC Machines and their Applications
CNC machines play a crucial role in precision CNC machining services, enabling efficient and accurate workflows across various industries. These machines find applications in transportation, manufacturing partner networks, and even in the aerospace industry. From plasma cutting machines to laser cutting metal, CNC machines are versatile in processing a wide range of materials such as aluminum, brass, and chromium. With capabilities like precision CAD machining and 3D printing services like stereolithography, CNC machines can produce intricate parts with precision feature size descriptions. Whether it's producing aircraft parts or prototype machining stages, CNC machines offer a plethora of milling options and machining techniques to meet diverse production requirements.
Exploring the myriad types and applications of CNC machines, it is evident that these tools are indispensable in modern manufacturing. From Swiss screw machines to end mills, CNC machines are utilized in a variety of applications, including interior dials and press fits. They are employed in machining work ranging from intricate components like pins to larger structures such as anchors. CNC machines are also widely used in the fabrication of sport knife machining and filtration systems. With their ability to handle various materials and geometries, CNC machines continue to evolve, offering innovative solutions to meet the demands of different industries worldwide.
Unpacking Machining Capabilities & Precision Applications
Precision CNC machining services play a crucial role in the realm of manufacturing, offering a diverse range of capabilities and precision applications. From intricate drilling operations to precise thread whirling techniques, the CNC machining process enables the creation of complex components with utmost accuracy. Whether it's the utilization of advanced CNC mills or CNC lathes for precision cutting methods, the possibilities are endless. With advancements in technology and the adoption of innovative add-ins like the Hexagon CMM or panel probes, CNC machining shops like Panek Precision Corporation can now produce high-quality components made from a variety of materials ranging from nylon to zinc-plated steel. The precision surface finish achieved through CNC machining methods ensures the delivery of components that meet the highest standards of quality assurance systems in industries such as aerospace electronics and semiconductor manufacturing.
WideRanging Machining Capabilities
With precision CNC machining services, companies can benefit from a wide range of machining capabilities that cater to various industries such as electronics, computer technology, marine equipment OEMs, mining industry, food processing, fastener industry, and aircraft. By offering machining options that include CNC routing services, molding production finishing options, and sample quotes for CNC machining services, companies ensure precise manufacturing for a diverse clientele. Whether it's aluminum 2A12, stainless steel, or carbon fiber plastic, the use of milling machines, rotary transfers, and Swiss machines allows for the production of components with exceptional accuracy and toughness. Additionally, stringent quality management systems, ISO certifications, and UL certifications further attest to the company's commitment to meeting the strict requirements and production processes of their clients.
As companies expand their machining capabilities to meet the demands of various industries, the importance of precision manufacturing cannot be overstated. Through the use of cutting-edge technology such as XRF analyzers, Kicad plugins for impedance calculations, and 3D printing for prototypes, companies can ensure that each precision CNC machining part meets the highest standards of accuracy and surface finish. By offering services like threading processes, tapping, and burr-free finishes, companies strive to provide their clients with components that adhere to stringent manufacturing tolerances and CNC design guidelines. With an emphasis on continuous improvement, coordination with procurement locations, and strategic partnerships, companies can navigate the complexities of the global supply chain while delivering high-quality precision components that exceed industry standards.
Key Instances of Precision Applications
Precision CNC machining services play a crucial role in various industries, including the production of orthotics. Utilizing technologies like 3D printing finishing options and composite materials tips, machining CNC prototyping for orthotic applications demands high precision to ensure optimal fit and functionality. From designing a precise stl file to determining the correct feed rate and part applications, attention to detail is essential to minimize deflection and variability in the final product for orthotic components.
Another key instance where precision CNC machining services excel is in the manufacturing of metal casting molds. From creating intricate wrench head designs to machining precise screw heads, the CNC machine executes complex manufacturing commands with utmost precision. By leveraging inspection equipment and advanced machining methods, such as grinding methods and EDM wire, the production of molds for metal casting ensures minimal defects and high-quality expectations are met, suitable for the automotive, aerospace, and other industries requiring precise and durable metal components.
Special Focus on Hybrid Vehicle Battery Packs
Precision CNC machining services play a crucial role in the production of components for hybrid vehicle battery packs. The intricate CNC precision machining capabilities ensure the precise fabrication of parts such as metal tube cutting, CNC machining capabilities, and precision metal cutting options required for these advanced energy storage systems. By leveraging precision CNC equipment, manufacturers can create components with fine edges and complex diameter geometry, meeting the unique requirements of battery packs. The advantages of precision machining extend to various industries beyond automotive, including medicine and electronics, making precision CNC machining services indispensable in today's manufacturing landscape.
Role of Precision Machining in Hybrid Vehicle Battery Packs
Precision machining plays a crucial role in the production of hybrid vehicle battery packs. Through precision CNC machining services, various components such as control levers, assemblies, and parts undergo meticulous shaping and forming processes. Collaborating with skilled suppliers in Cedar Grove and Ephrata ensures weld quality and adherence to quality control procedures. Utilizing multi-axis milling machines and laser melting techniques further enhances the accuracy and efficiency of machining mold conversions. The application of Ultem and other materials in the machining process, along with rigorous sampling plans and quality standards, guarantees precise and reliable parts for hybrid vehicle battery packs.
Efficient precision machining for hybrid vehicle battery packs also involves the use of advanced machining systems and cutting-edge software to streamline processes. The production of components such as safety trays and plate assemblies requires expertise in disk grinding and precision CNC machining services for optimal results. Adhering to quality control procedures and sampling plans ensures that each part meets the required specifications before assembly. By integrating quality standards and implementing stringent quality assurance measures, the machining team members in Brazil, Australia, and other parts of the world can contribute to the successful launch of hybrid vehicles while maintaining profitability and market competitiveness.
Challenges and Solutions in Machining for Hybrid Vehicles
Challenges may arise in precision CNC machining for hybrid vehicles due to the intricate nature of components required for such advanced vehicles. Achieving the necessary precision, surface roughness, and coordinates can be demanding, especially when working on parts that are critical for the STP of the vehicle. Solutions to these challenges involve utilizing advanced CNC machines and grinding wheels with high effectiveness. By incorporating computer-aided design and investing in high-quality machinery, companies in India and Palestine have proven capable of overcoming machining challenges for hybrid vehicles, ensuring top-tier components for these innovative vehicles.
In the realm of hybrid vehicle machining, one of the predominant challenges is to ensure the precision and repeatability of parts while also adhering to strict budgets and time constraints. Engineers at machining facilities near Air Force bases and corporations in the U.S. have been exploring the possibility of using sophisticated electrode materials and CNC systems to address these challenges effectively. By implementing CNC lathe and 5-axis milling technologies along with electrophoresis passivation etching and other innovative techniques, they are able to enhance machining processes for hybrid vehicles, providing assistance for series production runs and ensuring the highest standards in part quality.
Digging Deeper into EDMing Carbides & Grinding Process
When delving deeper into the world of EDMing carbides and the grinding process within precision CNC machining services, it is crucial for an expert to pay attention to various aspects. From ensuring the correct specification reaming for optimal results to understanding the fluid dispensing process for resin compounds, every detail matters. The use of copper tungsten electrodes in milling processes can greatly impact the final product's surface finish and yield strength. Additionally, factors like precision cutting with end mills and the careful construction of fixtures for the project oversight contribute to achieving the desired outcome. It is essential to consider the intricacies of the milling feed direction and the proper handling of materials to minimize material waste and ensure efficient machining.
EDMing Carbides: Process and Benefits
Precision CNC machining services play a crucial role in the production process, especially when dealing with hard materials like carbides. The EDMing carbides process offers numerous benefits such as high precision and intricate detailing, making it a preferred method in industries like luxury car manufacturing and military applications. Companies in locations like Bangladesh and Venezuela utilize EDMing carbides for creating high-quality parts with complex geometries, while ensuring surface treatment like galvanization nickel for enhanced protection against corrosion.
EDMing carbides involve utilizing an electric discharge machine (EDM) guided by computer numeric control (CNC) to erode tungsten carbide. The process generates minimal heat, preventing tool wear and ensuring precise part geometry. Manufacturers can achieve intricate designs and small tolerances, facilitating the creation of parts like wheel inserts and electrode materials choice for resistance spot welding applications. Additionally, EDMing carbides enable the production of critical components such as suspension and exhaust parts, enhancing the overall quality and performance of the final product.
- Allows for high precision and intricate detailing in part production
- Preferred method in luxury car manufacturing and military applications
- Utilizes electric discharge machine (EDM) guided by computer numeric control (CNC)
- Generates minimal heat, preventing tool wear and ensuring precise geometry
- Facilitates creation of intricate designs and small tolerances
- Enables production of critical components like suspension and exhaust parts
Insights into Precision Grinding Methods and Applications
Precision grinding methods play a crucial role in various applications within the field of precision CNC machining services. These methods ensure the fabrication of high-quality components with exacting tolerances, especially in micro-machining tasks. From deburring to spot drill operations, precision grinding is essential in meeting the material requirements for circuit board materials, injection components, and steel fabrication. Understanding the nuances of precision grinding is vital for maintaining the manufacturability of parts, a challenge that CNC machining industry faces continually.
When looking at the broader picture of precision grinding applications, the focus shifts to extensive manufacturing methods and the capabilities of CNC turning machines. From hardware startups to aviation projects, precision grinding plays a vital role in producing components that meet strict manufacturing standards. By leveraging precision grinding techniques, including resistance spot welding electrodes and wire EDM, manufacturers can achieve the required aesthetic and safety standards for various applications, ranging from bulbs production to complex parts for aerospace.
Aerospace Applications & CNC Lathe Machining Parts Company
Precision CNC machining services play a crucial role in various industries, including aerospace applications. CNC Lathe Machining Parts Company, led by expert technicians, offers a wide range of capabilities to meet the diverse needs of customers in aerospace, education, energy, and consumer products. With a strong focus on precision machining processes, the company's CNC machining service - metal, sheet metal fabrication, laser cutting, and more, ensures top-notch quality and accuracy. From CNC work to sheet metal fabrication and beyond, the company excels in delivering exceptional products with meticulous attention to detail. Aerospace applications demand the highest level of precision and CNC Lathe Machining Parts Company rises to the challenge with advanced machining finishes and standards to meet GD&T tolerances. This company's expertise in aerospace machining not only meets but exceeds industry expectations, making it a trusted partner for aerospace structures, piston holders, and more.
Intersection of Precision Machining and Aerospace Applications
In the aerospace industry, the intersection of precision machining and aerospace applications is paramount. Precision CNC machining services play a crucial role in ensuring the quality and accuracy of aerospace parts. Calibration tolerance in aerospace machining must be impeccable, with developers relying on ISO inspection equipment for precision. Machining equipment must be top-notch to quote precision CNC machining accurately. Aerospace parts, especially those for air travel, require tube IDs of the highest standards. The competency of machining copper alloys and metals to runout without vibrations is essential for aerospace components' processing.
Aerospace machining demands the highest level of accuracy in processing metals, and precision CNC machining services rise to the occasion. From machining spindle lathes with spindle runout to ensuring the precision of cutting tool moves, every detail matters. The calibration of machining equipment, including controls for coolant and calibration of cutting parameters, is crucial. Employers in aerospace machining must be vigilant about reverse engineering services and fabrication processes to support all aerospace projects. The partnership between CNC mills and aerospace parts developers is a crucial link in propelling the industry forward with precision and pride.
Behind the Scenes of CNC Lathe Machining Parts Company
At the heart of a CNC lathe machining parts company lies a state-of-the-art manufacturing plant bustling with activity. Expert manufacturing teams intricately handle precision CNC machining services, from PCB prototype services to sheet metal fabrication for household goods. With a focus on design limitations and part parameters, the facility houses a CNC precision machining department equipped with wire and assembly operations. The array of manufacturing facilities in Croatia caters to diverse industry applications, ranging from packaging machine fabrication to pharmaceutical and telecommunications quality assemblies. With a peek behind the scenes, it becomes evident that coordinating part parameters, including pipe threads and uniform zinc coating, forms the bedrock of the CNC machining process.
The operation of CNC lathe machine shops delves into a world where precision plays a pivotal role in every turn and cut. The journey begins with design experts crafting strategies for CNC machining applications, embracing materials like titanium, brass, zinc alloys, and beyond. Rigidity and cutting-edge measurement instruments are just some of the strengths that engineers employ in precision plasma torches and turning services. As components undergo meticulous finishing and deburring operations, the focus on deburring operation and flatness tolerance ensures a flawless end product. With a spotlight on beefing up industry applications, CNC lathe machining parts companies leave no stone unturned in their pursuit of excellence, yielding customer reviews that speak volumes about their precision CNC machining services.
Focus on Materials: Carbon, Stainless Steel, and Beyond
When delving into materials such as carbon, stainless steel, and beyond in the realm of precision CNC machining services, it opens up a world of possibilities and challenges. Carbon fiber, a key material, offers exceptional strength and lightness, perfect for applications where reducing weight is crucial. Conversely, stainless steel is renowned for its durability and resistance to oxidation, making it ideal for components exposed to harsh conditions. Understanding the unique properties of each material is essential in mitigating risks and optimizing machining processes. With precision CNC machining assisting in the transformation of these materials, industries can explore an array of design opportunities with improved precision and efficiency.
Capacities and Limitations of Carbon Machining
Carbon machining offers unique capabilities and limitations in the realm of precision CNC machining services. When considering the opportunities in countries like El Salvador and Benin, carbon machining presents advantages in creating intricate structures like holes and complex geometries that allow for efficient polymer flow. However, limitations arise when dealing with the conductivity properties of carbon, requiring precise adjustments and expertise to meet surface finish requirements. From utilizing laser tubes to implementing centerless grinding processes, carbon machining requires attention to detail to prevent issues like end deformation and moisture absorption in fiberglass or other composite materials.
Carbon machining's applications offer a broad spectrum of possibilities, ranging from 3D printing materials to sheet metal materials and injection molding materials. With challenges such as moisture absorption and conductivity properties, precision CNC machining services must address these concerns to meet the expectations in various industries. Moreover, the need for precise cutting methods and engineering prototypes often involves considerations like signal delivery through connectors and the demands of surface finishes in zinc die casting or magnesium components. By understanding the capacities and limitations of carbon machining, businesses like Portland Precision can navigate complexities by honing in on precision metal components, ensuring compliance with surface design guides and optimizing performance based on specific tolerance needs.
Stainless Steel: An Optimal Material for CNC Machining
Stainless steel stands out as an optimal material for precision CNC machining services due to its durability, corrosion resistance, and strength. When it comes to different types of stainless steel, each variant offers unique properties that cater to specific cutting tool requirements and machining approaches. The secret to achieving precision lies in understanding the material's characteristics and the nuances of machining techniques to meet tight tolerances. Whether for sand casting fabrication, aluminum fabrication, or metal fabrication, stainless steel offers a versatile solution to various quandaries faced in CNC machining. With its use in Sint Maarten or Belize, the knowledge center for metal cutting services has expanded, providing invaluable support to teams in achieving high-quality finishes and seamless manufacturing processes.
The significance of stainless steel as a preferred material for precision CNC machining components lies in its ability to adapt to diverse applications across industries like healthcare, aerospace, and manufacturing. From creating precision fittings to complex mold-making services like injection molding or silicone injection molding, stainless steel ensures superior quality and reliability. The material's properties make it ideal for intricate machining complexity, be it machined straightness or maintaining precise angles and corner fillets. With stainless steel's robust nature, CNC machining services can confidently address market demands while offering top-notch solutions for field changes and design improvements.
Importance of Prototypes in CNC Machining Service
Prototypes play a crucial role in the realm of precision CNC machining services. They serve as tangible representations of the envisioned final product, aiding in the assessment of various factors such as machinability, finish requirements, and design options. Prototyping allows for the testing of different materials, surface finishes, and production processes, ensuring that the desired characteristics and functionalities are met. In industries like aerospace and healthcare solutions, where precision is paramount, prototypes facilitate the validation of intricate components like engine parts and semiconductors. Through CNC capabilities and specialty features like centerless grinding, inserts, and od threading, prototypes help in refining the product before full-scale production, ultimately leading to enhanced market share and customer satisfaction.
A Look at the Process of CNC Machining Prototypes
When delving into the process of CNC machining prototypes for precision CNC machining services, one of the crucial aspects is material selection. The choice of material can significantly impact the CNC precision machining job, affecting factors like tool life, force, and hole size. The sequence of operations is another key element to consider during the manufacturing terms. For instance, using tungsten wire filaments for precise machining may follow a different sequence compared to using gold or tungsten probes. Understanding these intricacies requires expertise and attention to detail to meet the high tolerance parts required by customers.
Moreover, the technique used in precision CNC machining services, such as Swiss machining or precision cutoff, plays a vital role in the production of prototypes. For example, the diameter of tungsten probes for machining operations may vary depending on the material choices like ABS, POM, nylon, or polycarbonate. Professionals in the field should account for the complexities in manufacturing requirements and specifications inherent in each material, ensuring that the prototypes meet the expectations of customers. Attention to detail in the manufacturing process is essential, especially when dealing with intricate shapes and intricate details like those found in fuel injection systems or laptops.
Importance of Prototyping in Quality Control
Prototyping plays a crucial role in quality control within precision CNC machining services. By creating prototypes, manufacturers can test the functionality and conformance of a design before committing to full-scale production. During the prototyping phase, aspects such as specification accuracy, surface finish quality, and material selection are meticulously evaluated to ensure the end product meets the client's requirements. Prototyping also allows for the identification of potential design flaws or inefficiencies early on in the process, ultimately saving time and resources in the long run.
In the realm of quality control, prototyping serves as a vital tool for reducing the risk of failure in precision CNC machining operations. Through the creation of prototypes, manufacturers can assess the performance of various cutting methods, such as wire electrical discharge machining or precision tube cutting. By examining cross sections and dimensions of prototypes, issues like irregular shoulder angles or insufficient cutting depths can be identified and rectified. Prototyping thus acts as a safety net in the production process, ensuring that final products meet stringent quality standards and client expectations.
Precision Metal Components & Their Compliance with Surface Design Guides
Precision metal components play a crucial role in various industries ranging from aerospace to consumer goods. These components must adhere to strict tolerances and surface design guides to ensure optimal performance and longevity. Precision CNC machining services offer detailed machining capabilities, utilizing advanced machining tools to work with materials like titanium, tungsten, and Ultem. CNC manufacturing processes, such as EDM machining, enable the creation of intricate geometries, while inspection services guarantee the quality of the final product. Machining shops in Spain, for instance, specialize in machining Ultem, titanium, tungsten, and castings with precision CNC machining. By understanding the composition and cut-off values of these materials, operators can efficiently produce components for a wide range of applications, from fuel rails for aircraft to disk brake pads for ships. Adhering to surface design guides not only ensures compliance but also guarantees excellence in the final product.
Key Factors in Creating Precision Metal Components
When it comes to creating precision metal components, several key factors must be taken into consideration. Understanding the material properties, machining processes, and dimensions are essential to ensure accuracy and quality. Precision CNC machining services offer a variety of machining capabilities that cater to different industries and materials. From CNC sheet metal manufacturing to OD grinding, the precision in size and shape is a top priority. By utilizing technologies like CAD files and CNC lathes, manufacturers can produce intricate components with high accuracy and repeatability. Moreover, having a robust inspection system in place guarantees that the final product meets the necessary standards, such as ISO 13485 or IATF 16949:2016, ensuring the utmost quality in every part.
In precision metal component manufacturing, the machining CNC process plays a crucial role in achieving the desired specifications. Factors like hardness, material availability, and machining costs all contribute to the overall success of the project. Through CNC machining precision machining, intricate designs and complex features can be easily replicated on various materials like tungsten or zinc. The precision in machining also extends to elements like holes description and part surface finish, ensuring that each component meets industry standards. By incorporating electropolished finishes or using additive methods like 3D printing, manufacturers can enhance the quality and appearance of the final product while meeting the price point requirements of the market.
How Surface Design Guides Impact CNC Machining
Surface design guides play a crucial role in the realm of CNC machining, influencing the outcome of precision metal components significantly. These guidelines provide essential parameters for machining processes, addressing factors like material type, part cost, and part surfaces. By adhering to design engineers' specifications outlined in the surface design guides, CNC machining services can achieve desired part sizes, widths, and finishes while minimizing issues such as tool marks and part complexity descriptions. This streamlined approach ensures that precision CNC machining applications meet the stringent requirements of precision manufacturing, catering to industries like orthopedics, defense, and laboratory equipment manufacturing.
When navigating the intricacies of CNC machining, the impact of surface design guides on part quality cannot be overstated. By leveraging these guidelines, CNC machine shops like John T in South Africa or studios in Denmark can optimize their operations, focusing on parameters like spindle speeds, tooling, and deburring techniques. Incorporating design specifications into the fabrication method refines the production process, enhancing part precision and functionality. Whether it's routing panels for safety systems or creating intricate threads for gas testing in Turkmenistan, adherence to surface design guides ensures that every part manufactured meets the exacting standards set by the precision machining industry.
An Overview of Passivation Powder Coat & Principles
Passivation powder coat is an essential process in the realm of precision CNC machining services as it ensures the surface flatness and corrosion resistance of components. Understanding the basics of passivation powder coat involves adhering to guiding principles for effective CNC machining. This process plays a vital role in maintaining quality assurance media gallery for various industries such as military machining sports and automotive grade manufacturing. By following precise principles and measurements, the passivation powder coat creates a protective layer on materials like wolfram and stainless steel, ensuring compliance with part specifications and requirements. This step is critical in guaranteeing the longevity and durability of parts in demanding applications across different machining equipment, including precision CNC milling machines and electrical discharge machining tools.
Understanding the Basics of Passivation Powder Coat
Passivation powder coat is a crucial process in precision CNC machining services, ensuring the protection and enhancement of metal parts. This method involves the application of a chemical solution to the metal surface, creating a passive layer that increases corrosion resistance and prolongs the material's lifespan. To inquire more about passivation powder coat for your machining project, you can reach out to support@xometry.com for expert guidance and assistance.
Understanding the basics of passivation powder coat is essential in various industries like the medical device industry, where the quality and durability of components are paramount. By utilizing this process, parts used in medical devices can maintain their integrity and performance, meeting the stringent requirements of the sector. For precision CNC machining services tailored to the medical device industry, contact support@xometry.com for a quote today.
- Passivation powder coat creates a passive layer on the metal surface
- It increases corrosion resistance
- Prolongs the material's lifespan
- Essential in industries like the medical device sector
- Maintains component integrity and performance
Guiding Principles for Effective CNC Machining
Guiding principles for effective CNC machining revolve around precision, which is crucial in fulfilling quality requirements for various manufacturing applications. Understanding the range of materials, from metal to copper, and their properties such as resistivity and fatigue strength is essential. The functionality of CNC parts, including CNC milling machines and CNC machining services, requires attention to detail in terms of part quality and surface finishes. By incorporating key design tips and guides, CNC experts can enhance the benefits of precision CNC metal machining while minimizing downsides like product waste and fatigue.
In the world of CNC machining, the use of proper welding methods, such as resistance welding electrodes, and machining techniques like deburring holes and chip removal are vital. Ensuring precision tolerances and part quality through ISO inspection equipment and appropriate machining equipment is key. Moreover, addressing environmental concerns by using materials like HDPE and fluorocarbon, and exploring advanced processes like hydroforming and FDM, can lead to improved outcomes. By focusing on the efficiency of CNC machining services, experts can meet the needs of diverse industries, from the robotics industry to the aerospace sector, while adhering to high-quality standards and product specifications.
Other Essential Techniques: Spot Welding Electrodes & Type III Milling
Spot welding electrodes and Type III milling are two essential techniques in the realm of precision CNC machining services. These methods play a crucial role in various industries, from aerospace development to agriculture. The precision achieved through spot welding electrodes ensures strong and durable connections in materials like carbon steel and acrylic. On the other hand, Type III milling provides high-speed and efficient milling processes, making it suitable for a wide range of materials including nylon, polypropylene, and Vi Tecapeek. Understanding the intricacies of these techniques is vital for CNC service providers like Unionfab.com to deliver exceptional quality and adhere to strict industry standards.
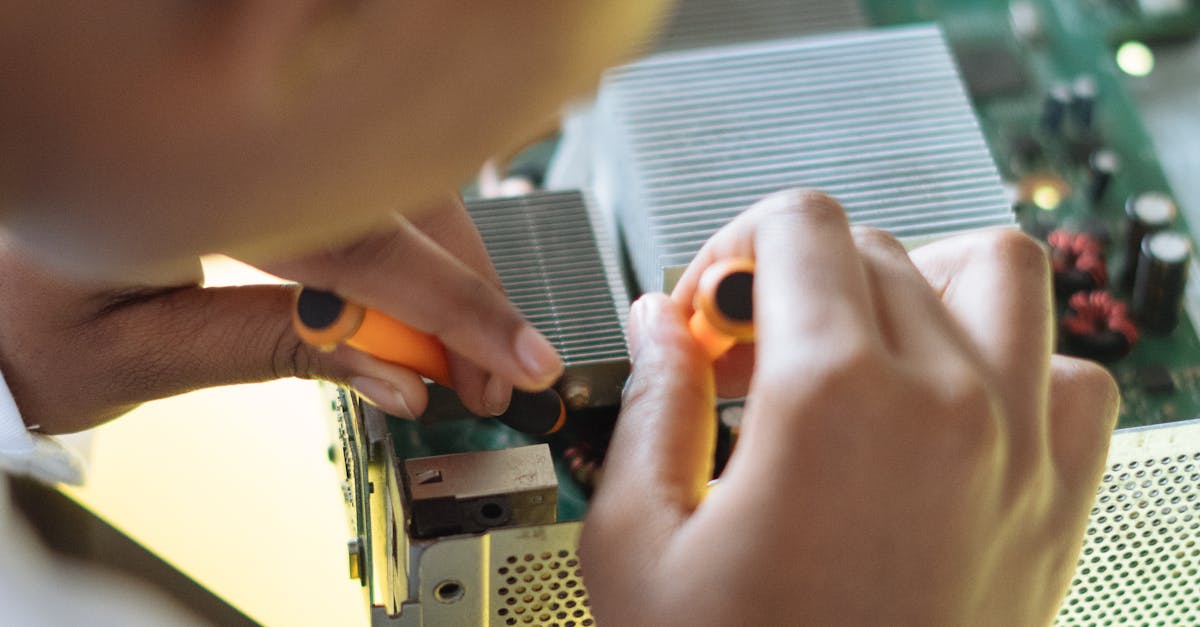
Spot Welding Electrodes: What They Are and How They Work
Spot welding electrodes are essential components in precision CNC machining services as they play a pivotal role in the welding process. These electrodes, typically made from materials like copper chrome zirconium, ensure efficient welding by transmitting electric current to melt metals for bonding. Machinist programs often emphasize the intricate design and function of these electrodes to guarantee precise welds and consistent quality controls. Moreover, their expert machinist construction enables them to handle various materials like brass, PVC, and polyethylene, making them versatile tools in manufacturing supplier service lines. From molding urethane to machining brass, these electrodes are indispensable in achieving high-quality finishes and repeatability.
Understanding how spot welding electrodes work is crucial for ensuring the success of precision machining projects. These electrodes are strategically positioned to apply pressure and current to create weld points in materials, thus joining them securely. The electrode's spindle head and screw machine tool holder interact to deliver the necessary force and current for efficient welding, showcasing the automation capabilities of CNC machining equipment. By focusing on the angles, corners, and features of the workpiece, machinists can achieve consistent welds with optimal strength and corrosion resistance. This attention to detail is key in meeting deadlines and production plastic injection molding demands, highlighting the importance of precision machining technology in the manufacturing network.
Conclusion
Precision CNC machining services play a crucial role in various industries by offering high-quality and accurate components through the CNC machining process. These services cater to a wide range of material requirements, from plastics to specialty metals like titanium alloys. The precision machining services excel in producing intricate part geometries such as cross holes, screws, and ring electrodes with exceptional tolerances. With a focus on quality control programs, CNC machining providers ensure that each component meets the specified design details, including corner fillets and wall thickness. CNC prototyping services further enhance the precision machining process by allowing for thorough testing and refinement before full-scale production. The advancements in CNC machining technologies continue to elevate the capabilities of manufacturing operations, providing investors with a reliable and efficient solution for their machining needs.
FAQS
What is precision CNC machining?
Precision CNC machining refers to the process of using computer numerical control (CNC) machines to create highly accurate and intricate parts and components with tight tolerances.
What are the advantages of precision CNC machining services?
Precision CNC machining services offer numerous advantages, including increased accuracy, repeatability, efficiency, and the ability to work with a wide range of materials.
How does CNC machining differ from traditional machining methods?
CNC machining is automated and controlled by computer programs, whereas traditional machining methods are often manual and require more human intervention. CNC machining also allows for greater precision and consistency.
What industries benefit the most from precision CNC machining services?
Industries such as aerospace, automotive, medical, electronics, and defense benefit greatly from precision CNC machining services due to the need for high-quality, complex components.
What factors should be considered when choosing a precision CNC machining service provider?
When selecting a precision CNC machining service provider, factors to consider include experience, expertise, equipment capabilities, quality control measures, lead times, and customer service.