Plastic Injection Molding vs Plastic CNC - Pros and Cons
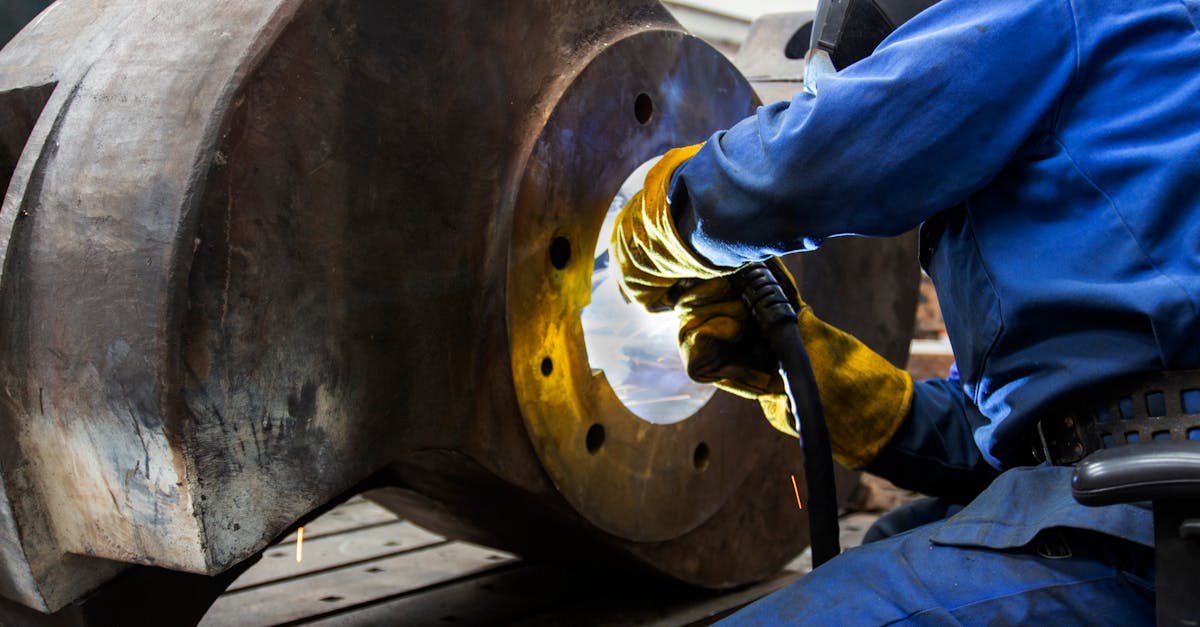
Table Of Contents
Lead Times
In the realm of manufacturing, lead times play a crucial role in determining the efficiency and effectiveness of production processes. Plastic injection molding and plastic CNC machining are two commonly utilized techniques in the industry, each with its own implications on lead times. When comparing the lead times between these two methods, it becomes evident that plastic CNC machining typically offers quicker turnaround times compared to plastic injection molding. This is due to the fact that CNC machining involves the direct fabrication of the desired product from a solid block of material, eliminating the need for mold creation and setup time.
On the other hand, plastic injection molding often involves more elaborate preparation processes, such as mold design, creation, and fine-tuning, which can contribute to longer lead times. Despite its potential for higher production volumes once the molds are set up, the initial lead time for plastic injection molding tends to be longer compared to plastic CNC machining. Therefore, when time-sensitive projects are at hand, opting for plastic CNC machining may be the more viable choice to ensure swift turnaround and efficient production.
Time from design to production
Plastic injection molding and plastic CNC are popular manufacturing processes with distinct timelines from design to production. In plastic injection molding, the time from design to production is generally longer compared to plastic CNC. This is because injection molding involves creating molds and setting up the machinery before the production of parts can begin. From initial design to final production, the process can take several weeks to complete, depending on the complexity of the project.
On the other hand, plastic CNC machining offers quicker turnaround times from design to production. CNC machines can often start producing parts shortly after the design has been finalized, leading to faster lead times compared to injection molding. With CNC machining, the need for molds is eliminated, allowing for a more streamlined production process. As a result, projects can be completed in a shorter timeframe, making CNC machining a preferred option for those seeking rapid manufacturing solutions.
Sustainability
When considering sustainability in plastic manufacturing processes like injection molding and CNC, it's crucial to assess their environmental impact. Plastic injection molding typically involves the use of a considerable amount of plastic material during production, which can generate waste and contribute to plastic pollution. On the other hand, plastic CNC machining often produces less waste due to its subtractive manufacturing process which cuts away excess material, making it a more sustainable option in terms of material usage.
In addition to material waste, the energy consumption of each process also plays a role in their overall sustainability. Plastic injection molding requires high amounts of energy to heat and melt the plastic materials, while CNC machining generates more localized heating during the cutting process. This energy consumption difference can impact the carbon footprint of each method, making it essential to consider energy efficiency alongside material waste when evaluating the sustainability of plastic manufacturing techniques.
Environmental impact
Both plastic injection molding services and plastic CNC processes have distinct environmental impacts that need to be duly considered. Plastic injection molding is known to generate more waste in the initial setup phase compared to plastic CNC, due to the creation of molds and tooling. However, once the molds are established, plastic injection molding generally produces less waste as it can efficiently produce large quantities of parts. Moreover, many plastic injection molding facilities have implemented recycling programs for excess plastic material, helping to reduce overall environmental impact.
On the other hand, plastic CNC machining typically generates less waste in the setup phase, as it does not require molds or tooling. However, the process produces more waste during the actual machining of the parts, as excess material is cut away to create the final product. Unlike plastic injection molding, recycling options for such waste in plastic CNC machining may be limited, leading to potential environmental concerns. Overall, both processes have their environmental trade-offs that must be considered when deciding on the most suitable manufacturing method for a given project.
Durability
Plastic injection molding and plastic CNC processes both offer varying degrees of durability in their finished products. In terms of durability, plastic injection molding tends to produce items that exhibit high strength and resilience. The nature of injection molding allows for complex shapes and intricate designs, which can contribute to the overall durability of the final product. Provided that the appropriate plastic material is selected, items manufactured through injection molding can withstand a range of external factors, making them suitable for long-term use in different applications.
On the other hand, plastic CNC machining also yields durable products, albeit with certain limitations compared to injection molding. CNC machining involves cutting away material from a solid block to create the desired shape, which can sometimes result in weaker points in the final product. While CNC-machined plastics can still be durable, the process may not always be suitable for producing items that require intricate designs or have complex geometries that demand uniform strength throughout.
Longevity of finished products
Plastic injection molding and plastic CNC are both viable manufacturing processes that yield products with varying levels of longevity. In terms of longevity, plastic injection molding typically produces products that are known for their durability and strength. The process involves injecting molten plastic into a mold cavity, resulting in a sturdy final product that can withstand wear and tear over an extended period. This durability makes plastic injection molded products ideal for applications requiring long-term use without significant degradation.
On the other hand, plastic CNC products can also exhibit impressive longevity. CNC machining involves cutting and shaping a solid block of plastic material to create the desired part. The precision and customization offered by CNC machining can result in products with high dimensional accuracy and structural integrity, contributing to their longevity. While CNC products may not always match the ruggedness of injection molded items, they excel in applications where intricate designs or complex geometries are crucial for the longevity of the finished product.
Post Production Options
Plastic injection molding and plastic CNC processes offer various post-production options to enhance the final appearance and functionality of the products. One key aspect to consider is the surface finishing methods available for each process. Plastic injection molding allows for a wide range of finishing options such as painting, texture application, and printing to achieve the desired aesthetic appeal. On the other hand, plastic CNC offers more limited finishing choices but excels in producing precise and smooth surfaces due to the subtractive manufacturing method. This is different than custom blow molding, for example.
Moreover, post-production options for plastic injection molding include the ability to mold intricate shapes and designs with high precision. This process provides versatility in adding features like undercuts, inserts, and overmolding, allowing for complex product configurations. Conversely, plastic CNC is better suited for simpler geometries and offers the advantage of quick adjustments and modifications during the production process. Overall, understanding the post-production options available for each manufacturing method is essential in making informed decisions based on project requirements and goals.
Surface finishing methods
Surface finishing methods play a crucial role in the overall appearance and functionality of plastic products manufactured through either plastic injection molding or plastic CNC processes. Both methods offer a variety of techniques to enhance the aesthetics and performance of the final products. Common surface finishing methods include painting, texturing, polishing, and coating. These methods not only improve the visual appeal of the products but also provide protection against wear and tear.
Post-production options such as surface finishing methods further add value to the plastic products by allowing manufacturers to customize them according to specific requirements. By selecting the appropriate finishing techniques, manufacturers can achieve desired textures, colors, and finishes that meet the needs of the target market. Additionally, surface finishing methods also help in improving the durability and longevity of plastic products, making them more resistant to external factors such as moisture, heat, and impact.