What are the work holding devices in CNC machines?
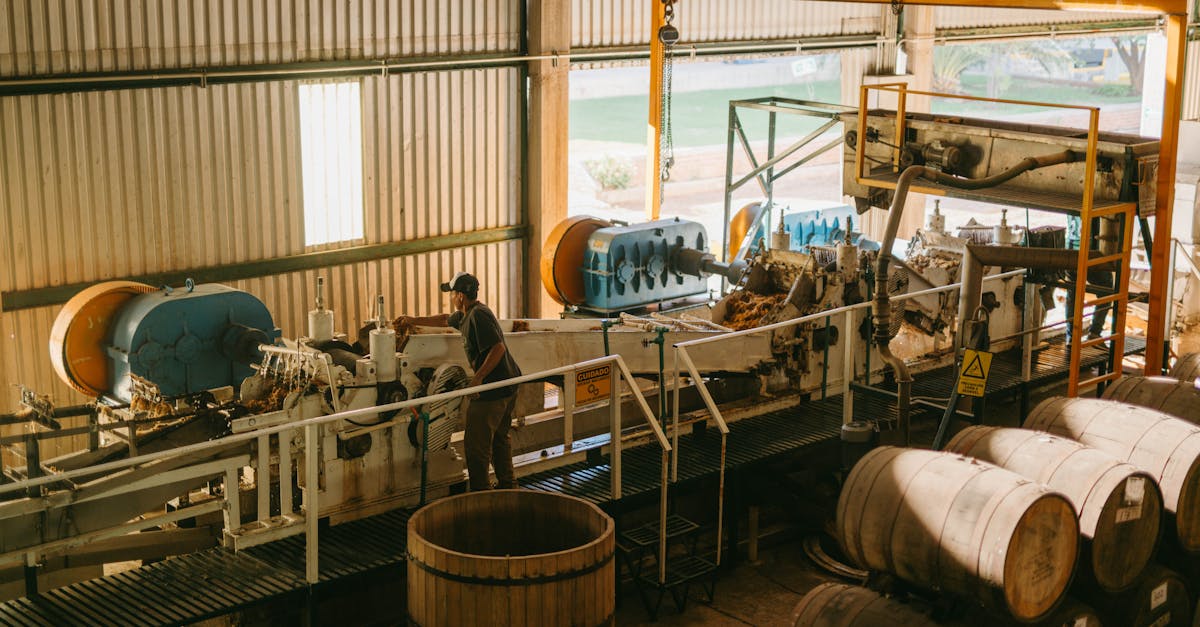
Table Of Contents
Selection Criteria for Work Holding Devices
Work holding devices in CNC machines play a crucial role in ensuring the accuracy and efficiency of machining processes. When selecting a suitable work holding device for a specific job, several factors must be taken into consideration. One key criterion is the type and size of the workpiece being machined. Different work holding devices, such as chucks, collets, or vises, are designed to accommodate various shapes and dimensions of workpieces.
Another important factor to consider when choosing a work holding device is the required level of precision for the machining operation. For high-precision machining tasks, a work holding device with tight tolerances and secure clamping mechanisms is essential to prevent any deviations or errors in the final product. Additionally, factors like accessibility for tooling, ease of loading and unloading the workpiece, and the overall stability of the setup should also be evaluated when deciding on the most suitable work holding device for a particular CNC machining job.
Continue to read this blog post for more great tips.
Pallets
Pallets are a common work holding device used in CNC machines to efficiently manage the machining process. They provide a versatile platform for securing workpieces during production, allowing for quick and seamless interchangeability within the machine. Pallet systems are particularly useful in high-volume manufacturing environments, where repetitive operations are required to be carried out with minimal downtime.
These work holding devices enable operators to preload multiple workpieces onto different pallets, reducing setup time between jobs and maximizing machine utilization. Pallets can also enhance overall production efficiency by allowing for simultaneous machining of multiple parts, leading to increased output and cost-effectiveness in CNC machining operations.
Factors Influencing Work Holding Device Choice in CNC Machining
Factors influencing work holding device choice in CNC machining include the type and size of the workpiece, the machining operations to be performed, and the desired level of precision. The geometry and material of the workpiece are crucial factors in determining the type of work holding device required. For complex shapes or delicate materials, specialized work holding devices such as vices, chucks, or collets may be necessary to securely hold the workpiece in place during machining.
Additionally, considering the cutting forces involved in the machining process is essential when selecting a work holding device. High-speed machining or heavy cutting may require more robust and rigid work holding devices to ensure stability and prevent vibrations that can affect the quality of the finished part. Moreover, the production volume and setup time must be taken into account when choosing a work holding device, as quick-change systems or modular setups can help reduce downtime and increase overall efficiency in CNC machining operations.
Tailstocks
Tailstocks are an essential component of work holding devices in CNC machines. They provide support and alignment for the workpiece, ensuring accuracy and precision during machining operations. Tailstocks are commonly used in turning and drilling processes to secure the workpiece in place and prevent any movement or deflection while the cutting tool is engaged.
One key feature of tailstocks is their ability to be adjusted to accommodate different sizes and shapes of workpieces. By easily adjusting the tailstock position, machinists can ensure that the workpiece is held securely and centered during machining. Additionally, tailstocks can be equipped with various accessories such as centers, arbors, and chucks to further enhance their versatility and adaptability to different machining requirements.
Tips for Efficient Work Holding in CNC Machines
To ensure efficient work holding in CNC machines, it is essential to carefully select the appropriate work holding device for the specific task at hand. One tip for achieving this is to consider the material of the workpiece, its size, shape, and the machining operations to be performed. By taking these factors into account, you can choose the right work holding device that provides optimal stability and precision during the machining process.
Another important tip for efficient work holding in CNC machines is to regularly inspect and maintain the work holding devices. Inspecting for wear and tear, ensuring proper lubrication, and replacing any damaged components can help prevent issues such as part movement or inaccuracies during machining. By keeping the work holding devices in good condition, you can enhance the overall effectiveness and productivity of CNC machining operations.
Mandrels
Mandrels are essential work holding devices used in CNC machining to securely clamp and support various types of workpieces during the manufacturing process. These devices play a crucial role in maintaining the accuracy and precision of the machining operation by providing a stable platform for the workpiece to be operated on. Mandrels can come in different designs and configurations, such as expanding mandrels, collet chucks, and hydraulic mandrels, each tailored to suit specific machining requirements.
The primary function of a mandrel is to center the workpiece and ensure concentricity during the machining operation. By using a mandrel, manufacturers can achieve consistent and reliable results when machining parts with intricate geometries or tight tolerances. Mandrels are particularly useful when working with fragile or thin-walled components that require extra support to prevent distortion or damage during the machining process.
FAQS
What are work holding devices in CNC machines?
Work holding devices are tools used to secure workpieces in place during machining operations in CNC machines.
What is the purpose of work holding devices in CNC machines?
The main purpose of work holding devices is to ensure the workpiece remains stable and accurately positioned during the machining process, resulting in precision and efficiency.
Can you provide examples of common work holding devices in CNC machines?
Some common work holding devices in CNC machines include vises, chucks, collets, fixtures, and clamps.
How do work holding devices contribute to the overall efficiency of CNC machining?
Work holding devices help to minimize vibrations, reduce errors, and enhance the repeatability of machining processes, leading to higher productivity and better quality outcomes.
Are there specific factors to consider when selecting work holding devices for CNC machining?
Yes, factors such as the size and shape of the workpiece, required precision, material being machined, and type of machining operation all influence the choice of work holding devices in CNC machining.