What does the term CNC stand for?
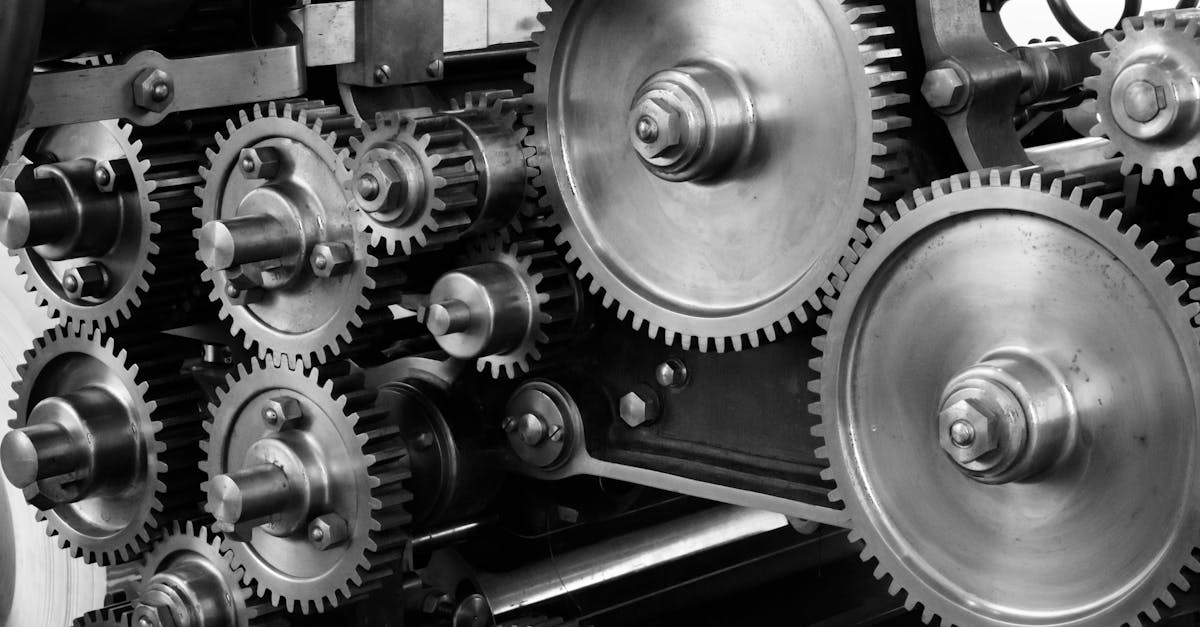
Table Of Contents
Common applications of CNC
CNC technology finds wide applications across various industries, revolutionizing manufacturing processes and enhancing precision. One of the common applications of CNC is in the automotive sector, where it is utilized for fabricating intricate components with high accuracy levels. The ability of CNC machines to work continuously without fatigue makes them ideal for producing complex parts consistently, contributing to the efficiency and quality of automobile production.
Moreover, the medical field benefits significantly from CNC technology, particularly in the production of customized prosthetics and implants. CNC machines enable the creation of precise and tailor-made medical devices according to the specific needs of patients, ensuring better functionality and comfort. The utilization of CNC in the medical sector highlights the versatility and adaptability of this technology in catering to diverse manufacturing requirements beyond traditional industrial settings.
See here for more great tips.
Aerospace industry
The aerospace industry relies heavily on CNC machining for the production of various components used in aircraft and spacecraft. CNC technology enables manufacturers to create complex and precise parts with high efficiency and accuracy, meeting the stringent quality standards required in the aerospace sector. From engine components to aircraft structures, CNC machines play a vital role in fabricating critical parts that contribute to the performance, safety, and reliability of aerospace vehicles.
With the increasing demand for lightweight materials and advanced designs in aerospace engineering, CNC machining continues to evolve to meet the industry's evolving needs. Innovations in CNC technology, such as multi-axis machining and high-speed cutting, have enabled manufacturers to push the boundaries of what is possible in terms of design complexity and part efficiency. As the aerospace industry continues to advance, the role of CNC machining will remain pivotal in shaping the future of aircraft and spacecraft development.
Future trends in CNC technology
The future trends in CNC technology are highly promising, with advancements in automation and digitalization leading the way. One significant trend is the integration of artificial intelligence (AI) in CNC systems, allowing for enhanced precision, efficiency, and adaptability in manufacturing processes. AI technologies can enable CNC machines to make real-time adjustments based on data analytics, leading to improved productivity and minimizing human error.
Another key trend in CNC technology is the development of smart factories and the Internet of Things (IoT) integration. This allows for seamless communication between CNC machines, sensors, and other systems within a manufacturing facility, leading to increased connectivity and optimization of production processes. The use of IoT in CNC technology enables remote monitoring, predictive maintenance, and real-time analytics, contributing to more efficient operations and reduced downtime.
Integration of AI in CNC systems
In recent years, the integration of artificial intelligence (AI) in computer numeric control (CNC) systems has revolutionized the manufacturing industry. AI technology has enhanced the capabilities of CNC machines by enabling them to perform complex tasks with a higher degree of precision and efficiency. By leveraging algorithms and machine learning, CNC systems powered by AI can optimize cutting paths, reduce material waste, and minimize production times.
Moreover, AI integration has also led to the development of predictive maintenance tools for CNC machines. These tools utilize AI algorithms to analyze machine performance data in real-time, identifying potential issues before they escalate into costly breakdowns. This proactive approach to maintenance not only improves machine uptime but also prolongs the lifespan of CNC equipment, ultimately reducing operating costs for manufacturers.
Training and education in CNC
Training and education in CNC play a crucial role in ensuring the proficiency of operators in using Computer Numerical Control machines effectively. Individuals interested in pursuing a career in CNC machining can benefit from formal training programs offered by technical schools, community colleges, and vocational institutions. These programs typically cover a wide range of topics including blueprint reading, machine operation, tooling, and programming.
Moreover, hands-on experience and practical training are essential components of CNC education. Many programs incorporate lab work and projects to provide students with real-world exposure to operating CNC machines. Additionally, continuous learning and staying updated with the latest advancements in CNC technology are vital for individuals looking to excel in this field.
Skills required for CNC operators
Skills required for CNC operators include a strong understanding of technical drawings and blueprints, as well as the ability to interpret complex instructions accurately. Attention to detail is crucial to ensure precision in machining processes. Additionally, problem-solving skills are essential for troubleshooting any issues that may arise during the production process.
Physical stamina is important as CNC operators often spend long hours standing and monitoring machines. Good hand-eye coordination is also necessary to operate equipment with precision and efficiency. Familiarity with computer programming and software is a key skill for CNC operators, as they need to input data, set parameters, and monitor the performance of CNC machines.
FAQS
What does CNC stand for?
CNC stands for Computer Numerical Control.
How does CNC technology benefit the aerospace industry?
CNC technology in the aerospace industry ensures precision manufacturing of complex components, leading to improved performance and safety of aircraft.
What are some future trends in CNC technology?
Future trends in CNC technology include the integration of Artificial Intelligence (AI) to optimize machining processes and enhance automation.
How is AI integrated into CNC systems?
AI is integrated into CNC systems to enable predictive maintenance, adaptive control, and real-time monitoring, improving efficiency and reducing downtime.
What skills are required for CNC operators?
CNC operators need to have a strong understanding of machining processes, attention to detail, problem-solving abilities, and proficiency in reading technical drawings and programming languages.