What is the most common workholding device?
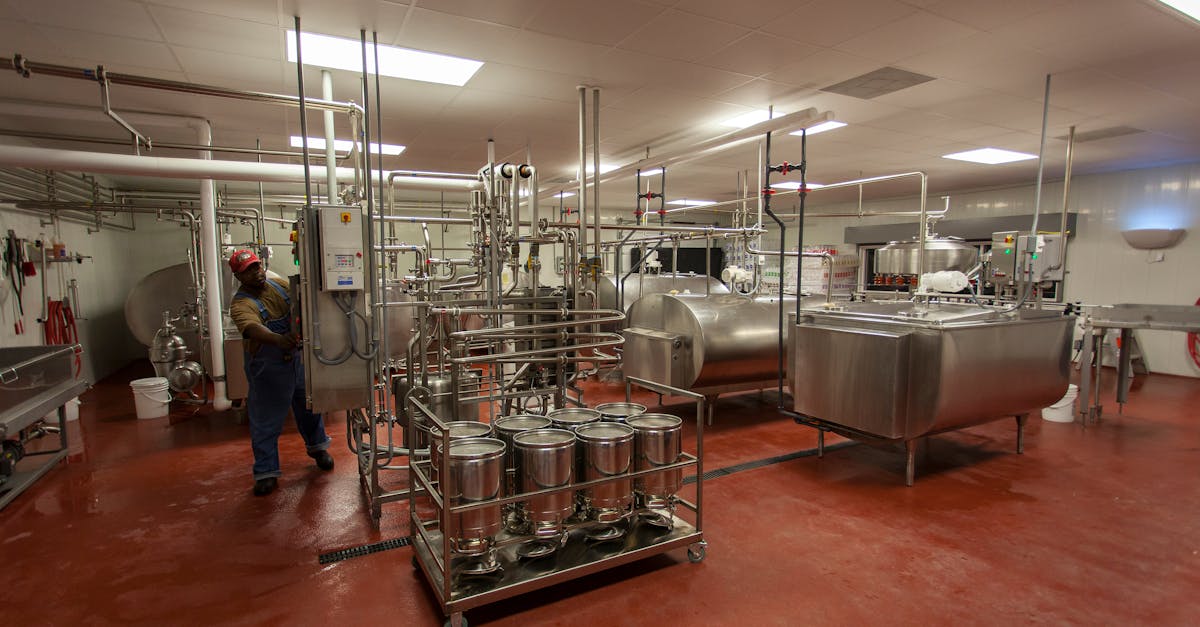
Table Of Contents
Emerging Technologies in Workholding Devices
Emerging technologies in workholding devices are continuously shaping the landscape of manufacturing industries. One notable advancement is the integration of smart sensors within workholding devices, allowing for real-time monitoring and adjustment of clamping forces and part positioning. This technology enhances precision and efficiency, ultimately contributing to improved product quality and production speeds.
Another innovative development in workholding devices is the utilization of magnetic workholding systems. These systems use electromagnetic forces to securely hold workpieces in place, eliminating the need for traditional clamps and fixtures. The magnetic workholding systems offer quick and easy setup, increased accessibility to the workpiece, and reduced changeover times between manufacturing processes. Implementing these cutting-edge technologies can revolutionize workholding processes, offering manufacturers a competitive edge in today's fast-paced industry.
Click here for additional info.
Automation in Workholding Processes
Automation is revolutionizing workholding processes in various industries by enhancing efficiency and precision. Through the use of automated systems, tasks that were once time-consuming and labor-intensive can now be completed with reduced human intervention. This not only speeds up production processes but also minimizes the risk of errors, resulting in consistent and high-quality outputs.
Moreover, automation in workholding processes allows for increased flexibility and adaptability in manufacturing operations. By utilizing advanced technologies such as robotics and sensors, workholding devices can adjust to different workpieces and machining requirements rapidly. This level of adaptability ensures that production processes can be easily customized to meet specific demands, leading to enhanced productivity and performance in modern manufacturing environments.
Safety Precautions When Using Workholding Devices
When using workholding devices in any industrial setting, it is crucial to prioritize safety precautions to prevent accidents and injuries. One of the most basic safety measures is to ensure that the workpiece is securely and properly clamped in place before starting any machining operations. Failure to do so can result in the workpiece becoming dislodged during operation, causing damage to the equipment or posing a risk to the operator.
Additionally, operators should always wear appropriate personal protective equipment (PPE) when working with workholding devices. This includes safety glasses to protect the eyes from any flying debris, gloves to safeguard the hands from sharp edges or hot surfaces, and ear protection if working with noisy machinery. Regularly inspecting workholding devices for wear and tear, as well as following manufacturer guidelines for usage and maintenance, are also essential safety precautions to ensure a safe working environment.
Personal Protective Equipment for Workholding Activities
Personal protective equipment (PPE) plays a crucial role in ensuring the safety of workers when using workholding devices. PPE includes items such as safety glasses, gloves, hearing protection, and steel-toed boots, all of which are essential in minimizing the risk of accidents and injuries in the workplace. Safety glasses protect the eyes from debris or sparks that may be produced during workholding activities, while gloves provide a barrier against sharp edges or hot surfaces.
Furthermore, hearing protection is vital in environments where noise levels are high, such as when using power tools or machinery with workholding devices. PPE not only safeguards workers from immediate hazards but also helps prevent long-term health issues that may arise from prolonged exposure to potentially harmful conditions. Employers should provide appropriate PPE and ensure that workers are trained on its correct usage and maintenance to maximize its effectiveness in safeguarding their well-being.
Importance of Proper Installation of Workholding Devices
Proper installation of workholding devices is crucial for ensuring the safety and efficiency of machining processes. When workholding devices are not installed correctly, there is a risk of workpiece slippage or tool breakage, which can lead to work accidents and costly damages. It is important to follow manufacturer guidelines and specifications during the installation process to guarantee that the workholding device is securely anchored and aligned for optimal performance.
In addition to preventing accidents, proper installation of workholding devices also contributes to improved accuracy and consistency in machining operations. When workholding devices are set up correctly, they help maintain the alignment of the workpiece throughout the machining process, resulting in precise and reliable outcomes. By paying close attention to the installation details and ensuring that the workholding device is properly positioned and secured, machinists can enhance the quality of their work and increase productivity in the workshop.
Aligning Workholding Devices for Optimal Performance
Aligning workholding devices is a critical step in ensuring optimal performance in machining operations. Proper alignment of workholding devices, such as vises or chucks, helps to secure the workpiece firmly in place during machining processes, reducing the risk of inaccuracies or errors. Misaligned workholding devices can result in poor surface finish, out-of-spec dimensions, and potential safety hazards. Therefore, taking the time to align workholding devices correctly is essential for achieving high-quality and precise machined parts.
One key aspect of aligning workholding devices is ensuring that they are parallel and perpendicular to the machine's axes. This alignment helps to maintain the accuracy of the machined part and prevents issues such as taper or out-of-roundness. Additionally, proper alignment allows operators to maximize the efficiency of their machining operations by reducing setup times and minimizing the need for rework. By paying attention to the alignment of workholding devices, machinists can improve the overall quality of their work and enhance the productivity of their manufacturing processes.
FAQS
What is a workholding device?
A workholding device is a tool or equipment used to secure a workpiece in place during machining or manufacturing processes.
What is the most common workholding device used in industries?
The most common workholding device used in industries is the vise. It is versatile, easy to use, and provides a secure grip on the workpiece.
How does a vise work as a workholding device?
A vise consists of two jaws that can be tightened or loosened to hold the workpiece firmly in place. It can be adjusted to accommodate different sizes and shapes of workpieces.
Are there different types of vises available for specific applications?
Yes, there are various types of vises such as bench vises, machine vises, drill press vises, and milling vises, each designed for specific machining operations and workpiece sizes.
What are some tips for using a vise safely?
To ensure safety when using a vise, always secure the workpiece properly, avoid over-tightening the jaws, use appropriate personal protective equipment, and follow the manufacturer's guidelines for operation.