What is the purpose of a workholding device?
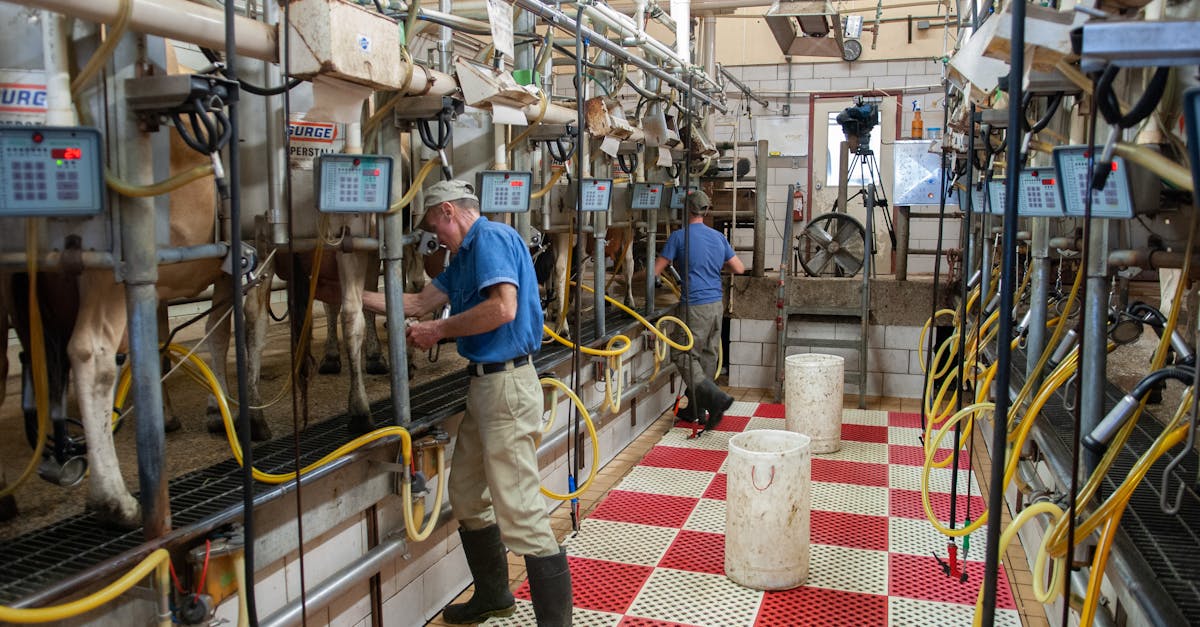
Table Of Contents
Safety guidelines for operating workholding devices
When operating workholding devices, it is essential to prioritize safety to prevent accidents and injuries in the workplace. One critical guideline is to always inspect the workholding device before and after each use to ensure it is in proper working condition. Any signs of wear and tear should be addressed immediately to avoid malfunctions that could lead to accidents.
Additionally, operators should familiarize themselves with the proper operating procedures of the specific workholding device they are using. This includes understanding how to securely fasten workpieces in place and making adjustments as needed to ensure stability during machining processes. Following these safety guidelines not only protects the operator but also contributes to the overall efficiency and quality of the manufacturing process.
This is an essential article for anyone looking to learn more about the topic.
Securing workpieces effectively to prevent accidents
Securing workpieces effectively is paramount in any manufacturing setting to prevent accidents and ensure the safety of operators. Workholding devices play a crucial role in this process by firmly gripping the workpiece in place during machining operations. By utilizing the appropriate workholding device for the specific task at hand, manufacturers can minimize the risk of workpieces becoming dislodged or moving unexpectedly, thereby reducing the likelihood of injuries and damage to equipment.
Properly securing workpieces also contributes to the overall quality and accuracy of the finished product. When workpieces are securely held in place, the chances of dimensional inaccuracies or defects resulting from movement or vibration are significantly reduced. This not only enhances the safety of the operation but also improves the efficiency and precision of the manufacturing process as a whole. By prioritizing effective workpiece securing techniques, manufacturers can create a safer working environment while achieving higher levels of product quality and consistency.
Innovations in workholding technology for enhanced efficiency
Innovations in workholding technology have significantly contributed to enhancing efficiency in manufacturing processes. Advanced precision workholding devices, such as hydraulic chucks and magnetic clamping systems, provide secure and stable grip on workpieces, allowing for precise machining operations. These innovative technologies eliminate the need for manual adjustments and ensure consistent part quality, leading to improved productivity and reduced setup times.
Furthermore, the integration of smart sensors and connectivity features in modern workholding devices has revolutionized manufacturing operations. Real-time monitoring of workpiece clamping forces and status enables operators to make informed decisions and prevent potential issues before they occur. The ability to remotely control and adjust workholding parameters using IoT technology not only enhances efficiency but also promotes a safer working environment. By embracing these technological advancements, manufacturers can optimize their production processes and stay ahead in today's competitive market.
Automated workholding systems and IoT integration
Automated workholding systems have revolutionized the manufacturing industry by enhancing efficiency and precision in the production process. These systems utilize advanced technology to securely grip and manipulate workpieces without the need for constant manual adjustments. By integrating Internet of Things (IoT) capabilities, manufacturers can monitor and control workholding devices remotely, leading to increased productivity and reduced downtime.
The IoT integration in workholding systems allows for real-time data collection and analysis, enabling predictive maintenance and proactive decision-making. This connectivity also enables seamless communication between different components of the manufacturing process, resulting in optimized workflow and reduced errors. As technology continues to advance, automated workholding systems will play a crucial role in streamlining production processes and maximizing output.
Costefficient solutions for smallscale manufacturing operations
Cost-efficient solutions play a crucial role in small-scale manufacturing operations, where budgets and resources are often limited. Implementing cost-effective workholding devices is essential to maximize productivity while keeping expenses at a minimum. Small businesses and workshops can benefit from utilizing simple yet efficient workholding solutions that cater to their specific needs without compromising on quality or safety.
One common approach is to opt for standardized workholding fixtures that are versatile and adaptable to a variety of workpieces. These modular setups allow for quick adjustments and reusability, reducing the need for frequent investments in custom fixtures. Additionally, investing in durable and reliable workholding devices can lead to long-term cost savings by minimizing the risk of errors, rework, and potential accidents in the manufacturing process. By prioritizing cost-efficient solutions, small-scale operations can optimize their production processes and remain competitive in the industry.
Modular workholding setups for flexibility and cost savings
Modular workholding setups offer manufacturers a cost-effective solution for achieving flexibility in their production processes while also maximizing cost savings. By utilizing interchangeable components and versatile fixtures, companies can easily adapt their workholding systems to accommodate different workpieces and machining operations. This adaptability not only enhances efficiency but also reduces the need for investing in multiple specialized workholding devices, ultimately leading to significant cost savings for small-scale manufacturing operations.
The ability to quickly reconfigure modular workholding setups allows manufacturers to streamline their workflow, minimize setup times, and improve overall productivity. This flexibility enables businesses to respond efficiently to changing production demands, such as varying batch sizes or the introduction of new product designs. With the modular approach, companies can easily customize their workholding systems to suit specific requirements, thus increasing operational efficiency and saving both time and resources in the long run.
FAQS
Why are workholding devices important in manufacturing processes?
Workholding devices are essential to securely hold workpieces in place during machining operations, ensuring accuracy and precision in the manufacturing process.
How do workholding devices contribute to workplace safety?
Workholding devices help prevent accidents by securely clamping the workpiece in place, reducing the risk of it coming loose during machining and causing injury to operators.
What are some common safety guidelines for operating workholding devices?
Safety guidelines for operating workholding devices include ensuring proper installation and maintenance, using appropriate clamping forces, and following manufacturer's instructions for safe operation.
How do innovations in workholding technology enhance efficiency in manufacturing?
Innovations in workholding technology, such as automated systems and IoT integration, streamline the manufacturing process by improving setup times, increasing productivity, and reducing human error.
What are cost-efficient solutions for small-scale manufacturing operations in terms of workholding devices?
Cost-efficient solutions for small-scale manufacturing operations include modular workholding setups that offer flexibility, scalability, and cost savings without compromising on precision and accuracy.