Why are CNC services so expensive?
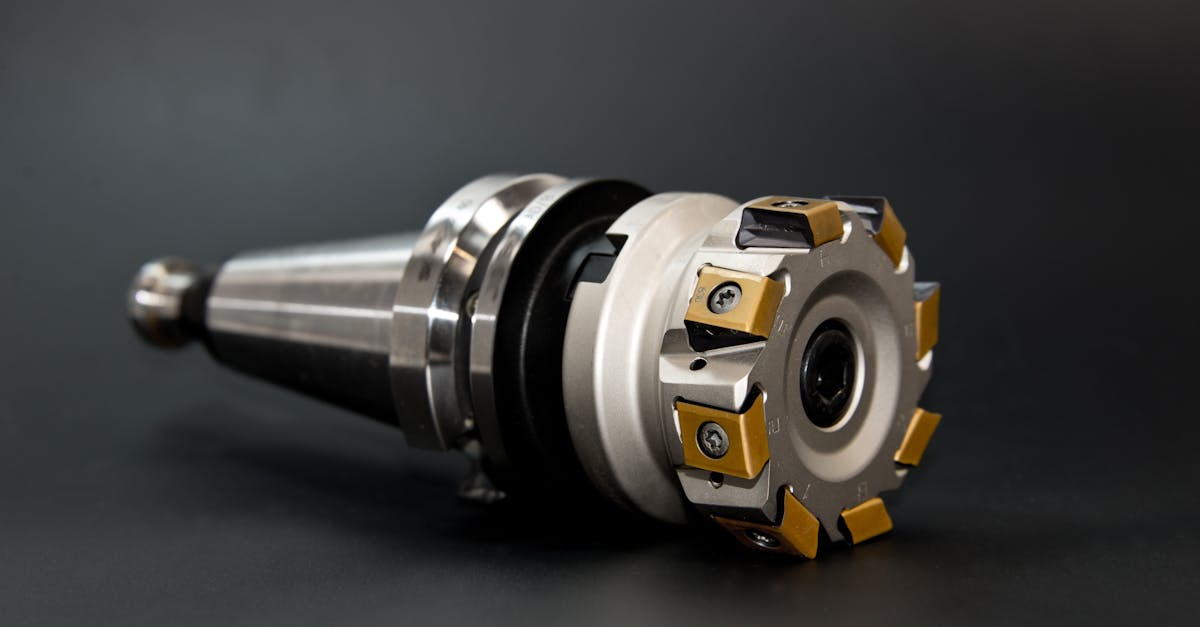
Table Of Contents
Market Demand and Supply Chain Dynamics
Market demand plays a significant role in determining the pricing structure of CNC services. The high demand for precision machining services contributes to the overall cost. As more industries require intricate parts with tight tolerances, the need for CNC services has increased substantially. This surge in demand has enabled CNC service providers to set higher prices, reflecting the value of their expertise and advanced technology.
Furthermore, supply chain dynamics also impact the cost of CNC services. The complexity of the supply chain, including raw material sourcing, tooling acquisition, and transportation logistics, adds to the overall expenses incurred by CNC service providers. Fluctuations in material prices and availability can lead to variations in service costs, as providers need to adjust their pricing strategies to accommodate these external factors.
Check out this site for more information.
Industry Trends and Availability
Industry trends play a crucial role in determining the availability of CNC services in the market. As technology continues to evolve rapidly, new demands and expectations emerge from various industries seeking efficient production processes. This constant push for innovation drives CNC service providers to stay abreast of the latest trends in order to meet the ever-changing needs of their clients.
Moreover, the availability of CNC services can also be influenced by market demand fluctuations. High demand periods may lead to a scarcity of service providers, resulting in increased prices and longer lead times for projects. Conversely, during low demand periods, there may be a surplus of CNC service providers, leading to price competition and more options for consumers. Understanding these industry trends and availability dynamics can help businesses make informed decisions when seeking CNC services for their manufacturing processes.
Research and Development in CNC Technology
Research and development in CNC technology plays a crucial role in driving innovation and advancements within the industry. Companies that invest heavily in R&D are able to stay ahead of competitors by introducing cutting-edge technologies and solutions to the market. The continuous improvement and refinement of CNC systems lead to enhanced performance, precision, and efficiency, which ultimately adds value to the end products and services offered to customers.
By allocating resources to research and development, CNC manufacturers can explore new materials, processes, and functionalities to meet the evolving demands of various industries. This strategic approach enables companies to adapt to changing market trends and customer requirements, positioning them as industry leaders in the highly competitive landscape of CNC services. Through ongoing R&D efforts, companies can push the boundaries of what is possible with CNC technology, opening up new possibilities for applications across different sectors and driving further growth and expansion in the market.
Innovation and Advancements
Innovation and advancements play a key role in the pricing of CNC services. As technology continues to evolve and improve, CNC machines are equipped with more advanced features and capabilities that allow for increased precision, efficiency, and quality in manufacturing processes. These innovations often require significant investments in research and development, which are ultimately reflected in the cost of the services provided.
Furthermore, staying at the forefront of technological advancements in the CNC industry involves continuous training and education for operators and technicians. As new technologies are introduced, professionals must undergo training to familiarize themselves with the latest tools and techniques. This ongoing investment in skills development adds to the overall cost of providing CNC services, contributing to the higher prices charged to customers.
Overhead and Operational Expenses
Overhead and operational expenses play a significant role in determining the cost of CNC services. These expenses encompass a variety of costs incurred by CNC service providers to ensure the smooth operation of their business. From administrative salaries and insurance premiums to equipment maintenance and software licenses, the overhead and operational expenses associated with running a CNC service can quickly add up.
Moreover, maintaining a state-of-the-art facility equipped with the latest machinery and technology contributes to the overhead costs. CNC service providers often invest a substantial amount of capital in establishing and maintaining a modern workspace that meets industry standards. Additionally, utility bills, such as electricity and water usage, also factor into the operational expenses of running a CNC service. By accounting for these overhead and operational costs, CNC service providers ensure the efficiency and quality of their services, albeit at a higher price point.
Facility Costs and Utility Bills
Facility costs and utility bills are significant factors contributing to the overall expenses of CNC services. Operating a facility equipped with advanced CNC machinery requires substantial financial investment. From leasing or purchasing the space to maintaining and upgrading the infrastructure, these costs accumulate and are reflected in the pricing of CNC services. Moreover, the usage of high-powered machinery and precision tools in CNC operations demands a considerable amount of electricity, which adds a substantial burden to utility bills. Maintaining optimal temperature and humidity levels within the facility further contributes to the operational costs that are ultimately passed on to the customers.
When considering the total operational expenses of a CNC service provider, facility costs and utility bills play a critical role in determining the pricing structure. The cost of rent or mortgage, property taxes, insurance, and maintenance of the facility all directly impact the overall expenses incurred by the business. In addition, utility bills including electricity, water, and gas add to the financial obligations that CNC service providers must manage. These expenses are essential for the smooth functioning of CNC operations, ensuring that the facility is equipped to deliver high-quality services to meet the demands of the market.
FAQS
Why do CNC services tend to be expensive?
CNC services are often expensive due to various factors such as market demand, supply chain dynamics, industry trends, research and development costs, innovation, overhead expenses, and facility costs.
How does market demand affect the cost of CNC services?
The high demand for CNC services can drive up the prices as CNC machines are in high demand for manufacturing various products efficiently and accurately.
What role do research and development play in the cost of CNC services?
Research and development in CNC technology require significant investment, which can contribute to the overall cost of CNC services as companies strive to stay competitive by adopting the latest technology.
Why are overhead expenses a factor in the pricing of CNC services?
Overhead expenses such as salaries, maintenance costs, and insurance can significantly impact the cost of providing CNC services, leading to higher prices for customers.
How do facility costs and utility bills influence the cost of CNC services?
The expenses associated with running a CNC facility, including rent, utilities, and maintenance, are factored into the pricing of CNC services, contributing to the overall cost for customers.