How much does CNC cutting cost per hour?
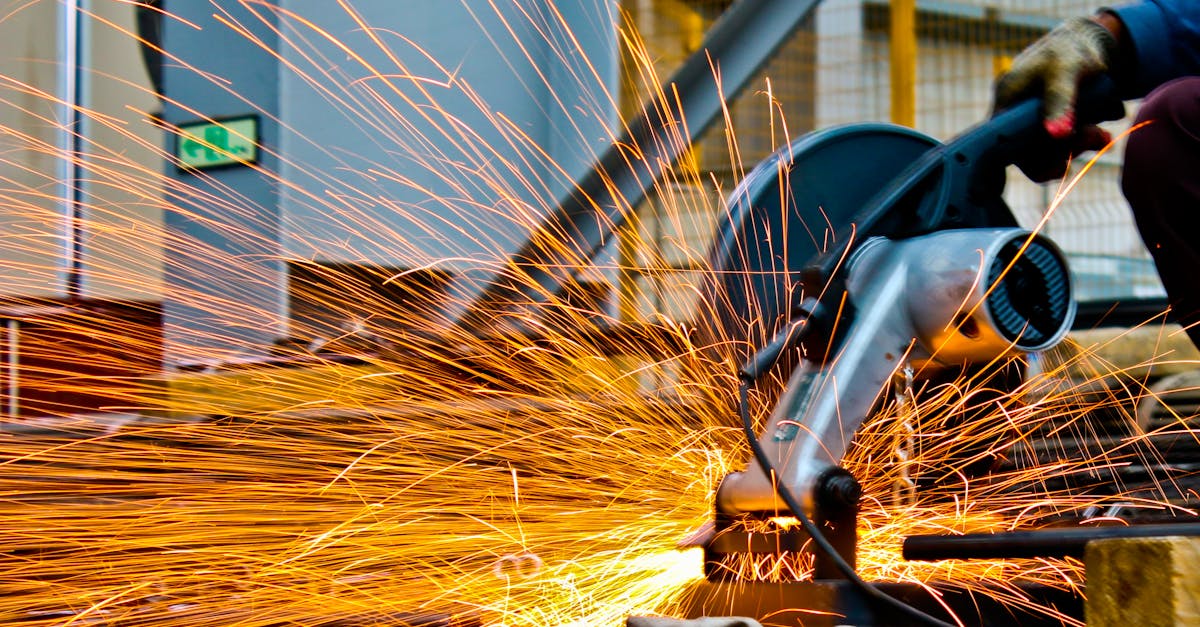
Table Of Contents
Additional Services
When it comes to CNC cutting services, additional services can significantly impact the overall cost per hour. These services may include design consultation, material sourcing, rush orders, and custom finishes. Design consultation services ensure that your project is planned and executed efficiently, while material sourcing services help in obtaining the right materials for the job. Rush orders, although convenient, usually incur additional charges due to the expedited nature of the service. Custom finishes, such as powder coating or painting, can enhance the final look of your product but will add to the overall cost.
Moreover, some CNC cutting service providers may offer value-added services such as assembly, packaging, or shipping assistance. These additional services can save you time and effort but come at an extra cost. It's essential to evaluate the need for these services based on your project requirements and budget constraints. By understanding the impact of additional services on the total cost per hour, you can make informed decisions and choose the services that best suit your needs.
Finishing and Quality Control
When it comes to CNC cutting, the finishing and quality control processes play a crucial role in the overall cost and quality of the final product. After the cutting process is complete, the next step involves finishing the edges, removing any burrs, and ensuring that the dimensions are accurate according to the design specifications. This step often requires skilled labor and specialized equipment, adding to the overall cost per hour of CNC cutting services.
Quality control is another essential aspect of CNC cutting, as it ensures that the final product meets the required standards and specifications. This process involves thorough inspections, measurements, and testing to detect any defects or deviations from the design parameters. Implementing rigorous quality control measures not only adds to the cost per hour but also enhances the reliability and consistency of the CNC cutting services being provided.
Geographic Location
The geographic location of a CNC cutting service provider plays a significant role in determining the overall cost per hour. Operating costs such as labor, utilities, and rent can vary greatly depending on the region. For example, a CNC cutting service located in a major city with high living expenses may charge more per hour compared to a similar service in a smaller town with lower overhead costs.
Furthermore, transportation expenses can also impact the pricing of CNC cutting services. Providers located in remote areas may have higher costs associated with shipping raw materials and delivering finished products to clients. In contrast, companies situated in industrial hubs or close to major transportation routes may have lower transportation expenses, which can result in a more competitive pricing structure for their services.
Overhead and Facility Costs
Overhead and facility costs significantly contribute to the overall expenses associated with CNC cutting services. These expenses encompass a wide range of factors, including rent or mortgage payments for the facility, utility bills such as electricity and water, insurance premiums, property taxes, and general maintenance costs. Additionally, expenses related to maintaining a safe working environment, including safety equipment, training programs, and compliance with regulatory standards, are also part of the overhead and facility costs.
Furthermore, the location of the CNC cutting facility can greatly influence the overhead costs. Operating in regions with higher costs of living or where commercial real estate prices are steep can substantially increase the overhead expenses. Conversely, establishing the facility in areas with lower overhead costs can offer a competitive advantage in pricing CNC cutting services. It is essential for businesses to carefully assess and manage overhead and facility costs to maintain a sustainable and profitable operation in the CNC cutting industry.
Machine Maintenance and Downtime
Machine maintenance is a crucial aspect that significantly impacts the overall cost of CNC cutting services per hour. Regular maintenance of CNC machines is essential to ensure optimal performance and prevent unexpected breakdowns. Scheduled maintenance helps in detecting and resolving potential issues before they escalate, reducing the downtime of the machine and ultimately cutting down on costs related to repairs and lost production time.
Downtime, on the other hand, can have a notable impact on the cost per hour of CNC cutting. Unscheduled downtime due to machine malfunctions or breakdowns can disrupt the workflow, leading to delays in completing projects within the specified timeframe. Minimizing downtime through proactive maintenance measures can enhance the efficiency of CNC operations, ensuring smooth production processes and cost-effectiveness in the long run.
Efficiency and Utilization Rates
Efficiency and utilization rates play a crucial role in determining the overall cost of CNC cutting per hour. A high level of efficiency means that the machine is operating at its maximum potential, producing more output in less time. This directly impacts the cost per hour, as the more efficiently the machine operates, the lower the cost tends to be. It is essential for businesses to constantly monitor and improve their efficiency and utilization rates to ensure that they are getting the most value out of their CNC cutting operations.
Factors that influence efficiency and utilization rates include the skill level of the operators, the complexity of the cutting tasks, and the quality of the machine itself. Proper training of operators can significantly improve efficiency, as they will be able to operate the machine more effectively and make fewer mistakes. Additionally, utilizing the machine for longer periods without breakdowns or maintenance issues can also contribute to higher utilization rates, ultimately reducing the cost per hour of CNC cutting. By focusing on improving these rates, businesses can better control their expenses and optimize their CNC cutting processes for maximum productivity.
FAQS
How is the cost of CNC cutting per hour calculated?
The cost of CNC cutting per hour is typically calculated based on factors such as machine maintenance, operator wages, overhead costs, and material expenses.
What are some additional services that may affect the cost of CNC cutting per hour?
Additional services such as design work, programming, rush orders, and expedited shipping can impact the overall cost of CNC cutting per hour.
Does the geographic location of a CNC cutting service provider affect the hourly cost?
Yes, the geographic location can play a role in determining the hourly cost of CNC cutting services, as labor and overhead costs vary by region.
How does machine maintenance and downtime impact the cost of CNC cutting per hour?
Machine maintenance and downtime can increase the cost of CNC cutting per hour, as repairs, parts replacement, and lost production time can add to overall expenses.
What role do efficiency and utilization rates play in determining the cost of CNC cutting per hour?
Efficiency and utilization rates are crucial factors in determining the cost of CNC cutting per hour, as higher efficiency and utilization can help reduce overall costs by maximizing machine output.