What is CNC precision machining?
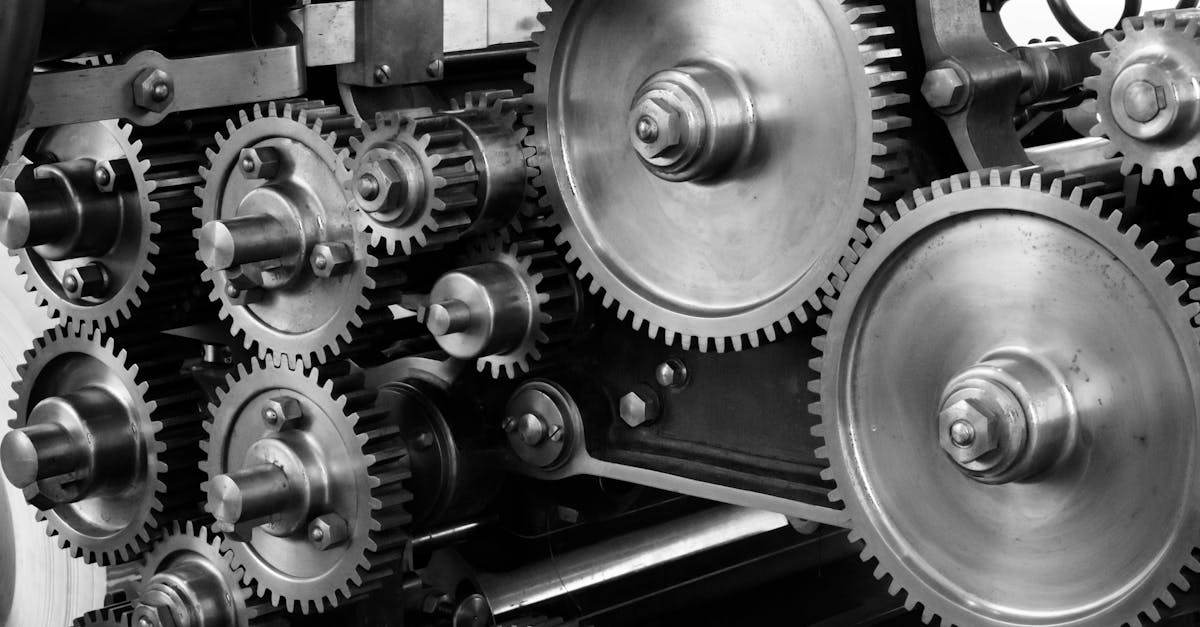
Table Of Contents
Quality Control in CNC Precision Machining
Quality control is paramount in CNC precision machining to ensure that final products meet the required specifications and standards. Through the use of advanced technologies and meticulous inspection procedures, manufacturers can maintain high levels of quality throughout the production process. One key aspect of quality control in CNC precision machining is the implementation of rigorous inspection and testing procedures to monitor the accuracy and consistency of manufactured parts.
Furthermore, advancements in CNC precision machining have enabled the integration of the Internet of Things (IoT) to enhance quality control measures. By incorporating IoT devices and sensors into machining equipment, manufacturers can gather real-time data on various parameters such as temperature, vibration, and tool wear. This data not only allows for immediate adjustments to be made to optimize machining processes but also facilitates predictive maintenance to prevent potential quality issues before they occur.
Inspection and Testing Procedures
Inspection and testing procedures are crucial stages in the CNC precision machining process. These procedures are implemented to ensure that the manufactured parts meet the required specifications and quality standards. Precision measuring tools such as micrometers, calipers, and coordinate measuring machines are commonly used to verify the dimensions and tolerances of the machined parts.
In addition to dimensional inspections, testing procedures involve conducting various tests to assess the mechanical properties of the components. Tests may include hardness testing, tensile testing, and impact testing to evaluate the strength, durability, and performance of the machined parts. By adhering to rigorous inspection and testing protocols, manufacturers can guarantee the quality and reliability of the products produced through CNC precision machining.
Advancements in CNC Precision Machining
Advancements in CNC precision machining have significantly enhanced the efficiency and accuracy of manufacturing processes. One key development is the integration of Internet of Things (IoT) technology into CNC machines. This allows for real-time monitoring and data analysis, leading to improved decision-making and increased productivity on the factory floor.
Another major advancement in CNC precision machining is the utilization of artificial intelligence (AI) algorithms. These AI systems can optimize machining parameters, predict tool wear, and even detect potential defects before they occur. By harnessing the power of AI, manufacturers are able to achieve higher levels of precision and quality in their machined components.
Integration of Internet of Things (IoT)
The integration of the Internet of Things (IoT) in CNC precision machining has revolutionized the industry by enabling machines to communicate with each other and with external systems. This connectivity allows for real-time monitoring of machines, predictive maintenance, and remote troubleshooting. Through IoT integration, manufacturers can optimize production processes, reduce downtime, and enhance overall efficiency.
Furthermore, IoT sensors embedded in CNC machines collect vast amounts of data, which can be analyzed to identify patterns, predict potential issues, and improve decision-making. By harnessing the power of data analytics, manufacturers can gain valuable insights into their operations, leading to increased productivity and cost savings. The seamless connectivity facilitated by IoT in CNC precision machining marks a significant advancement in the industry, paving the way for a more interconnected and intelligent manufacturing environment.
Future Trends in CNC Precision Machining
Future trends in CNC precision machining are continuously evolving with the integration of cutting-edge technologies. One prominent trend is the growing utilization of artificial intelligence (AI) within CNC machining processes. AI algorithms can analyze vast amounts of data to optimize tool paths, reduce machining time, and enhance overall efficiency. This automation not only improves precision but also minimizes human error, leading to higher-quality end products.
Additionally, the integration of the Internet of Things (IoT) in CNC precision machining is another significant trend shaping the industry. IoT technology enables machines to communicate with each other in real-time, monitoring performance, predicting maintenance needs, and maximizing productivity. This connectivity allows for remote monitoring and control, offering manufacturers greater flexibility and efficiency in their machining operations.
Artificial Intelligence in CNC Machining
Artificial intelligence (AI) is making significant strides in the field of CNC machining. CNC machines are becoming more intelligent and capable of self-optimization through the integration of AI algorithms. These algorithms can analyze vast amounts of data in real-time, enabling the CNC machines to make decisions autonomously and adjust machining parameters for optimal performance.
One of the key benefits of AI in CNC machining is predictive maintenance. By leveraging AI algorithms, CNC machines can predict potential issues before they occur based on historical data and patterns. This proactive approach helps minimize downtime, reduce maintenance costs, and improve overall efficiency in CNC precision machining processes.
FAQS
What is CNC precision machining?
CNC precision machining is a manufacturing process that utilizes computer numerical control (CNC) machines to create intricate and precise components from various materials such as metal, plastic, or wood.
How does CNC precision machining differ from traditional machining methods?
CNC precision machining is automated and computer-controlled, allowing for higher levels of accuracy, repeatability, and efficiency compared to traditional manual machining methods.
What are the benefits of using CNC precision machining?
Some benefits of CNC precision machining include increased productivity, consistency in quality, reduced lead times, and the ability to produce complex geometries that may be difficult to achieve with manual machining.
What types of materials can be used in CNC precision machining?
CNC precision machining can be used with a wide range of materials, including metals like aluminum, steel, and titanium, as well as plastics, composites, and wood.
How can I ensure the quality of parts produced through CNC precision machining?
To ensure quality, it is important to implement rigorous quality control measures, including regular inspection and testing procedures, adherence to industry standards, and leveraging advancements in technology such as the integration of the Internet of Things (IoT) and artificial intelligence.
Related Links
Why are CNC services so expensive?How much does CNC machining cost per hour?