How much does CNC machining cost per hour?
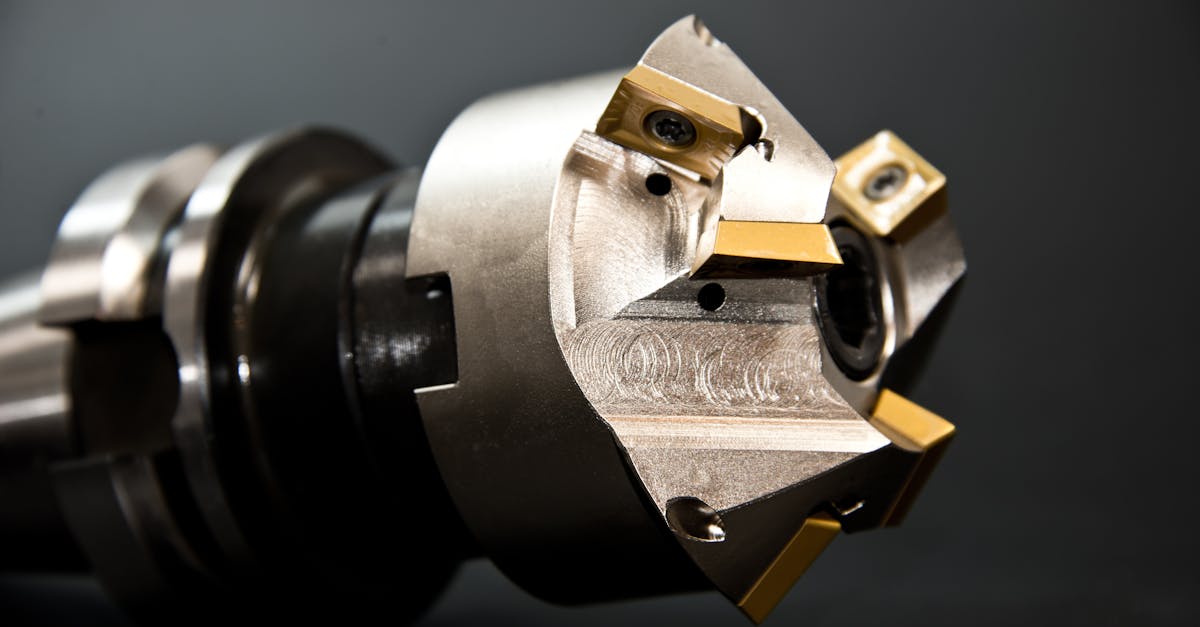
Table Of Contents
Additional services that impact CNC machining cost
Understanding the various additional services that can impact CNC machining costs is essential for businesses looking to optimize their production expenses. A crucial factor to consider is the complexity of the design and the level of precision required. Intricate designs with tight tolerances often require specialized tools and longer machining times, ultimately driving up the overall cost. Additionally, certain materials may be more challenging to machine, resulting in increased wear on cutting tools and requiring more frequent tool changes, which can add to the total machining cost.
Another important aspect to consider is the desired finishing options for the final product. Finishing processes such as polishing, anodizing, or powder coating can significantly impact costs. These additional services require extra time, labor, and materials, all of which contribute to the overall CNC machining expenses. The choice of finishing options should be carefully evaluated to ensure they align with the project requirements while also being mindful of the associated cost implications. By understanding the impact of these additional services on CNC machining costs, businesses can make informed decisions to optimize their production processes and achieve cost-efficiency in their operations.
Finishing options
When it comes to finishing options in CNC machining, there are several choices available to meet the desired surface finishes and appearances for the products. One common finishing method is anodizing, which provides a protective oxide layer on the surface of the material and can also enhance its aesthetics through coloring options. Anodizing is suitable for aluminum parts and can offer improved corrosion resistance as well.
Another popular finishing option is powder coating, which involves applying a dry powder onto the surface of the material and then curing it to create a durable and attractive finish. Powder coating is known for its versatility in color options, excellent durability, and resistance to scratches, chipping, and fading. It is a cost-effective finishing choice for various metal parts in CNC machining projects.
Outsourcing vs. inhouse CNC machining costs
When comparing outsourcing versus in-house CNC machining costs, there are various factors to consider in determining the most cost-effective option for your business. Outsourcing CNC machining services can sometimes be a more cost-efficient choice, especially for small businesses or projects with low production volumes. By outsourcing, you can avoid the high upfront costs associated with purchasing and maintaining CNC machines, as well as the expense of hiring and training specialized staff.
However, in-house CNC machining also has its advantages in terms of cost control and flexibility. By having CNC machines on-site, you have greater control over the production process and can make adjustments more quickly. Additionally, for high-volume production runs, in-house CNC machining can be more cost-effective in the long run as you eliminate the markup costs associated with outsourcing. Consider the specific needs and scale of your projects when deciding between outsourcing and in-house CNC machining to make the most cost-effective choice for your business.
Pros and cons of outsourcing
Outsourcing CNC machining can provide a range of benefits for businesses. One of the main advantages is cost savings. By outsourcing, companies can often access lower labor costs in countries where manufacturing expenses are comparatively cheaper. This can lead to significant savings on CNC machining projects, especially for large-scale production runs. Additionally, outsourcing can also offer access to specialized expertise and technology that may not be available in-house, allowing businesses to take advantage of the latest advancements in CNC machining.
On the other hand, outsourcing CNC machining also comes with its own set of challenges. One major concern is the potential loss of control over the production process. When a company outsources machining services, it may have less oversight and input into how the work is carried out. This lack of direct control can sometimes result in issues with quality or delays in project timelines. Moreover, communication barriers due to language differences or time zone disparities can also present obstacles when working with an outsourced CNC machining provider.
Tips for optimizing CNC machining costs
When aiming to optimize CNC machining costs, one crucial aspect to focus on is the design for manufacturability principles. By adhering to these guidelines, you can ensure that the product is designed in a way that maximizes efficiency during the machining process. This includes factors such as minimizing the number of tool changes, reducing the complexity of the design where possible, and selecting materials that are cost-effective yet suitable for the intended application.
In addition to design considerations, another effective strategy for optimizing CNC machining costs is to leverage the capabilities of the CNC machine to the fullest extent. This involves maximizing the toolpath efficiency, reducing unnecessary movements, and utilizing the appropriate cutting speeds and feeds for the materials being used. By fine-tuning these parameters and implementing best practices for CNC machining, you can significantly improve productivity and reduce overall machining costs.
Design for manufacturability principles
Design for manufacturability principles are essential in ensuring cost-effective CNC machining. By designing parts with manufacturability in mind, you can reduce machining time, material waste, and overall production costs. Simple designs with fewer intricate features are generally easier and cheaper to manufacture using CNC machining processes. When designing parts, consider factors such as the selection of materials, tolerances, and the complexity of shapes to optimize manufacturability.
Additionally, incorporating standard features like fillets, chamfers, and standard hole sizes can streamline the machining process and minimize the need for specialized tooling. Designing parts with uniform wall thickness and avoiding sharp corners can also enhance machinability and reduce the risk of errors during the manufacturing process. By following these design principles, you can not only improve the quality and efficiency of CNC machining but also lower the overall cost per hour of production.
FAQS
How is CNC machining cost per hour calculated?
CNC machining cost per hour is typically calculated based on factors such as machine setup time, material costs, operator labor costs, overhead expenses, and any additional services required.
What are some common additional services that can impact CNC machining costs?
Additional services such as complex programming, specialty tooling, rush orders, and specific finishing options can impact CNC machining costs.
What are some finishing options that may affect CNC machining costs?
Finishing options like anodizing, powder coating, polishing, or specialized coatings can add to the overall cost of CNC machining due to the additional time and materials required.
When considering CNC machining costs, what are the pros and cons of outsourcing versus keeping it in-house?
Outsourcing CNC machining can often be cost-effective for smaller production runs or complex projects, while keeping it in-house may be more cost-effective for larger volume production runs or projects requiring tight quality control.
How can I optimize CNC machining costs for my projects?
To optimize CNC machining costs, consider design for manufacturability principles, utilize standard materials and tooling, streamline production processes, and explore options for bulk ordering or scheduling to reduce overall costs.
Related Links
How much does CNC cutting cost per hour?precision cnc machining services