Is there money in CNC machining?
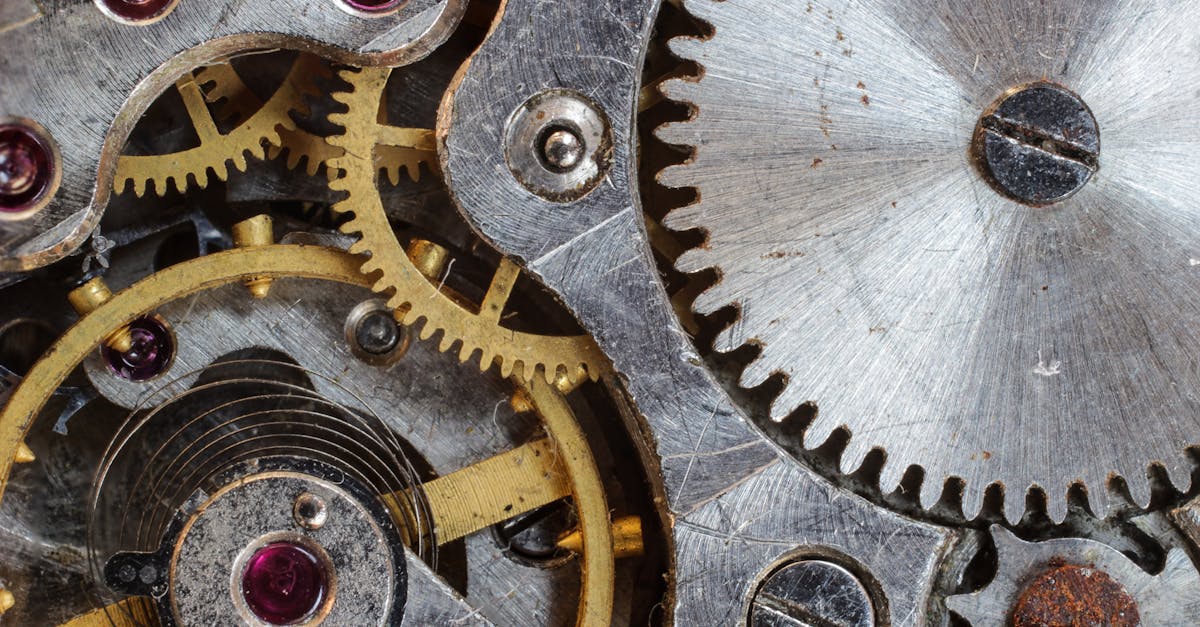
Table Of Contents
Advancements in CNC Technology
Advancements in CNC technology have transformed the manufacturing industry, enabling precision and efficiency like never before. The integration of automation, artificial intelligence, and machine learning has revolutionized the way CNC machines operate, enhancing productivity and quality control. These technological advancements have not only streamlined production processes but also reduced the margin of error, leading to cost savings for businesses.
Moreover, the advent of 5-axis CNC machines has further expanded the capabilities of CNC machining, allowing for more complex and intricate designs to be produced with higher accuracy. The improved flexibility and versatility offered by these advanced machines have opened up new possibilities for manufacturers to create innovative and customized products for a wide range of industries. Overall, the continuous advancements in CNC technology have paved the way for enhanced precision, speed, and reliability in manufacturing processes.
Continue reading this article for more information.
Automation and Industry 4.0
Automation and Industry 4.0 have revolutionized the CNC machining industry by introducing advanced technologies that streamline processes and increase efficiency. Manufacturers are now able to automate tasks that were previously time-consuming and labor-intensive, allowing for higher production rates and improved precision. This shift towards automation has also led to reduced costs and minimized errors, ultimately enhancing the overall competitiveness of CNC machining businesses in the global market.
Industry 4.0 technologies such as Internet of Things (IoT), artificial intelligence, and data analytics have enabled CNC machining companies to collect and analyze vast amounts of data in real-time. Through predictive maintenance and smart monitoring systems, manufacturers can proactively address machine malfunctions and optimize production schedules. This proactive approach not only reduces downtime but also extends the lifespan of equipment, resulting in increased productivity and profitability for CNC machining businesses.
Challenges Faced in the CNC Machining Industry
The CNC machining industry faces several challenges that hinder its growth and potential profitability. One significant issue is the persistent skills gap in the workforce, with a shortage of skilled machinists and operators who can effectively operate CNC machines. This gap leads to decreased productivity, longer lead times, and higher production costs, ultimately impacting the bottom line of businesses operating in this sector.
Another challenge in the CNC machining industry is the constant need for investment in advanced technology and equipment to stay competitive. With rapid advancements in CNC technology, companies must continuously upgrade their machinery to keep up with industry standards and meet evolving customer demands. This requirement for consistent investment poses a financial strain on businesses, particularly smaller companies that may struggle to afford the latest equipment and software.
Skills Gap and Training Needs
One significant challenge faced by the CNC machining industry is the growing skills gap among workers. As technology continues to advance, there is a pressing need for workers who possess the technical expertise required to operate CNC machines effectively. Many companies are finding it challenging to recruit and retain skilled workers who can keep up with the rapidly changing demands of the industry.
To address this skills gap, training programs and educational initiatives are essential. Providing comprehensive training to both new and existing employees can help bridge the skills deficiency and ensure that workers have the knowledge and competencies needed to succeed in the CNC machining field. Investing in training not only benefits individual workers by enhancing their skill sets but also contributes to the overall competitiveness and growth of the industry.
Sustainability Practices in CNC Machining
Sustainability practices in CNC machining are becoming increasingly important as the industry continues to grow. Companies are now focusing on reducing waste and implementing recycling initiatives to minimize the environmental impact of their operations. By incorporating sustainable practices into their processes, CNC machining companies can contribute to a more eco-friendly manufacturing sector.
Efforts to reduce waste in CNC machining include optimizing material usage and cutting down on energy consumption. Recycling initiatives involve reusing scrap materials and packaging wherever possible. These sustainable practices not only benefit the environment but also have the potential to improve the overall efficiency and cost-effectiveness of CNC machining operations in the long run.
Waste Reduction and Recycling Initiatives
In the CNC machining industry, waste reduction and recycling initiatives play a crucial role in promoting sustainability practices. Companies are increasingly realizing the importance of minimizing waste and maximizing resources to reduce their environmental footprint. Through the implementation of efficient waste management systems, CNC machining businesses can significantly decrease their impact on the environment.
Recycling initiatives within the CNC machining sector involve the collection and processing of materials such as metals, plastics, and other raw materials used in the manufacturing process. By reusing these materials or converting them into new products, companies can not only reduce the amount of waste sent to landfills but also conserve valuable resources. Additionally, recycling initiatives in CNC machining contribute to cost savings by decreasing the need to purchase new materials, making it a win-win situation for both the environment and the bottom line.
FAQS
Is CNC machining a profitable business?
Yes, CNC machining can be a profitable business due to its high precision, efficiency, and ability to produce complex parts.
How can advancements in CNC technology impact the profitability of a CNC machining business?
Advancements in CNC technology can lead to increased productivity, improved quality of parts, and reduced production costs, ultimately contributing to the profitability of a CNC machining business.
What challenges are commonly faced in the CNC machining industry that could affect the financial aspect of the business?
Challenges such as skills gap, competition, rapid technological changes, and fluctuating material costs can impact the financial stability of CNC machining businesses.
How can sustainability practices in CNC machining contribute to the financial success of a business?
Implementing sustainability practices such as waste reduction, energy efficiency, and recycling initiatives can not only enhance the brand image of a CNC machining business but also lead to cost savings in the long run.
What role does automation and Industry 4.0 play in improving the profitability of CNC machining businesses?
Automation and Industry 4.0 technologies can streamline operations, increase production efficiency, reduce human error, and optimize resource utilization, all of which can positively impact the profitability of CNC machining businesses.