What is a workholding fixture?
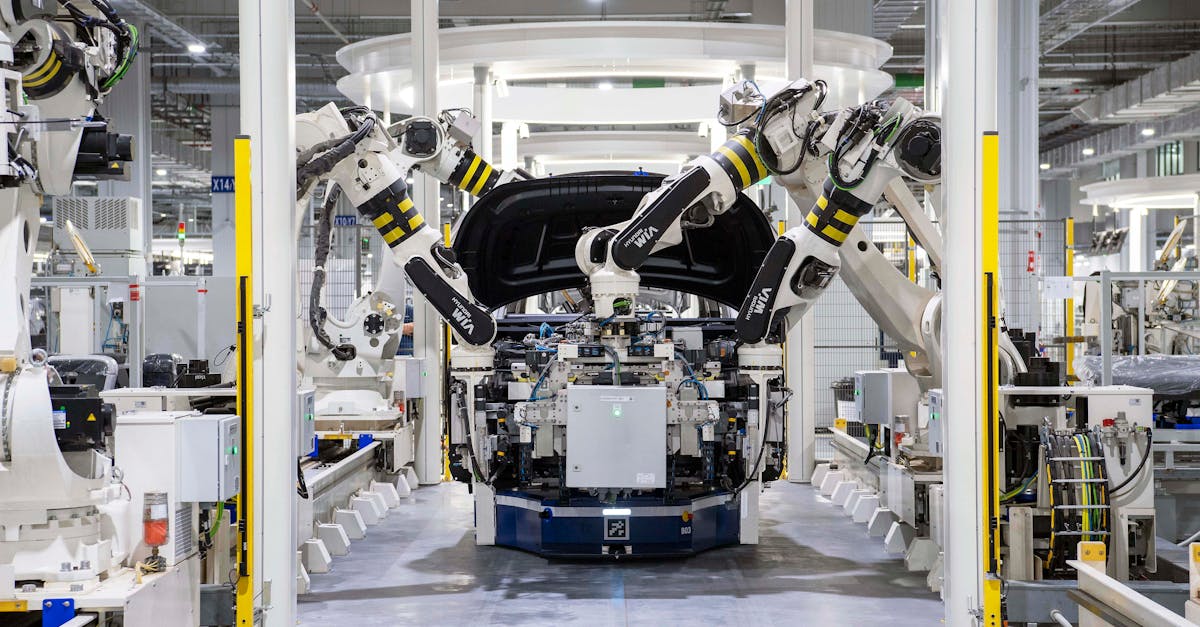
Table Of Contents
Common Applications of Workholding Fixtures
Workholding fixtures find widespread use in various industries where precision machining is crucial. One common application of workholding fixtures is in the automotive sector, where they are employed in the manufacturing of engine components, transmission parts, and chassis elements. The fixtures provide a stable and secure platform for machining processes, ensuring high accuracy and repeatability in the production of these critical automotive parts. Additionally, workholding fixtures are extensively utilized in the aerospace industry for the fabrication of components such as turbine blades, aircraft structural parts, and landing gear elements. In this sector, the fixtures play a vital role in maintaining strict tolerances and achieving intricate geometries required for aircraft components.
Another significant application of workholding fixtures is in the medical device manufacturing sector. These fixtures are indispensable for producing orthopedic implants, surgical instruments, and medical equipment with precise dimensions and surface finishes. By securely holding the workpiece in place during machining operations, workholding fixtures enable manufacturers to meet stringent quality standards and ensure the reliability of medical devices used in healthcare settings. Furthermore, workholding fixtures are also prevalent in the electronics industry for fabricating components like circuit boards, connectors, and semiconductor devices. The fixtures aid in achieving precise alignments and dimensions critical for the functionality and performance of electronic products.
Machining Processes
Machining processes involve the use of workholding fixtures to securely hold the workpiece in place during various machining operations. These fixtures are essential for ensuring accuracy and precision in processes such as milling, drilling, turning, and grinding. By securely clamping the workpiece in the desired position, workholding fixtures enable machinists to perform intricate cuts and shaping with consistency and repeatability.
In milling operations, for example, workholding fixtures are used to hold the workpiece in place while the cutting tool removes material to achieve the desired shape or finish. Similarly, in drilling processes, fixtures securely position the workpiece so that holes can be accurately drilled to the required depth and diameter. Workholding fixtures play a crucial role in maintaining stability and alignment during machining processes, ultimately contributing to the quality of the finished part.
Design Considerations for Workholding Fixtures
When designing workholding fixtures, one crucial consideration is ensuring stability and rigidity. The fixture should be able to securely hold the workpiece in place during machining processes to prevent any movement or vibrations that could affect the accuracy of the final product. This requires careful planning of the fixture's material, design, and clamping mechanisms to withstand the cutting forces and tool vibrations that occur during machining. Additionally, the fixture's design should provide ample support to the workpiece to minimize deflection and ensure consistent machining results.
Another important design consideration for workholding fixtures is versatility. Fixtures should be designed to accommodate a range of workpiece sizes and shapes to maximize their utility in various machining operations. This involves incorporating adjustable features such as movable jaws, sliding components, or modular clamping elements that can be easily configured to suit different workpieces. By designing fixtures with versatility in mind, manufacturers can increase their efficiency and flexibility in production processes, ultimately leading to improved productivity and cost-effectiveness.
Stability and Rigidity
Stability and rigidity are two crucial aspects to consider when designing workholding fixtures for machining processes. A stable fixture ensures that the workpiece remains securely in place during cutting operations, minimizing vibrations and potential inaccuracies in the finished part. Rigidity is equally important as it helps to maintain the precise position of the workpiece under the forces exerted during machining, reducing the risk of deflection and maintaining tight tolerances.
When designing workholding fixtures, engineers must consider the material and construction of the fixture to achieve the necessary stability and rigidity. Factors such as the geometry of the fixture, the type of clamping mechanism used, and the overall structural integrity all play a role in ensuring that the fixture can effectively hold the workpiece in place without any unwanted movement. By prioritizing stability and rigidity in the design phase, manufacturers can enhance the overall machining accuracy and productivity of their operations.
Installation and Maintenance of Workholding Fixtures
Installation and maintenance of workholding fixtures are crucial aspects that can greatly impact the efficiency and effectiveness of machining processes. Proper installation ensures that the fixture is securely attached to the machine tool, preventing any movement or vibration during operation. It is essential to follow the manufacturer's guidelines and recommendations to ensure accurate alignment and positioning of the workholding fixture.
Regular maintenance is key to ensuring the longevity and optimal performance of workholding fixtures. This includes regular cleaning, inspection of components for wear and tear, and lubrication of moving parts. Any signs of damage or wear should be addressed promptly to prevent any negative impact on the machining process. Additionally, following best practices for maintenance can help prevent unexpected breakdowns and costly repairs, ultimately contributing to increased productivity and quality of workpieces.
Best Practices
When it comes to using workholding fixtures effectively, following best practices is key to ensuring optimal performance. One important best practice is to always thoroughly inspect the fixture before use to check for any signs of wear or damage. This step is crucial in preventing any accidents or errors during the machining process. Additionally, regular maintenance and cleaning of the fixture is essential to prolong its lifespan and maintain its accuracy.
Furthermore, it is recommended to follow the manufacturer's guidelines and recommendations for the specific workholding fixture being used. This includes adhering to recommended torque settings for clamps and ensuring that the workpiece is securely held in place. By following these best practices, operators can enhance the efficiency and precision of their machining processes while also ensuring the safety of both the equipment and personnel.
FAQS
What is a workholding fixture?
A workholding fixture is a tool used in machining processes to securely hold a workpiece in place during operations like drilling, milling, or grinding.
What are the common applications of workholding fixtures?
Workholding fixtures are commonly used in industries such as automotive, aerospace, and manufacturing for tasks like precision machining, assembly, and quality control.
What are the design considerations for workholding fixtures?
When designing workholding fixtures, factors such as stability, rigidity, material selection, and ease of setup and maintenance should be taken into account to ensure efficient and accurate machining processes.
How important is stability and rigidity in workholding fixtures?
Stability and rigidity are crucial in workholding fixtures as they ensure that the workpiece remains secure during machining operations, reducing the risk of errors and improving overall precision.
What are some best practices for the installation and maintenance of workholding fixtures?
Best practices for workholding fixture installation and maintenance include regular inspection for wear and damage, proper cleaning and lubrication, and following manufacturer guidelines for setup and adjustment to prolong the life and effectiveness of the fixture.
Related Links
What is workholding in CNC?cnc workholding fixtures