What is workholding in CNC?
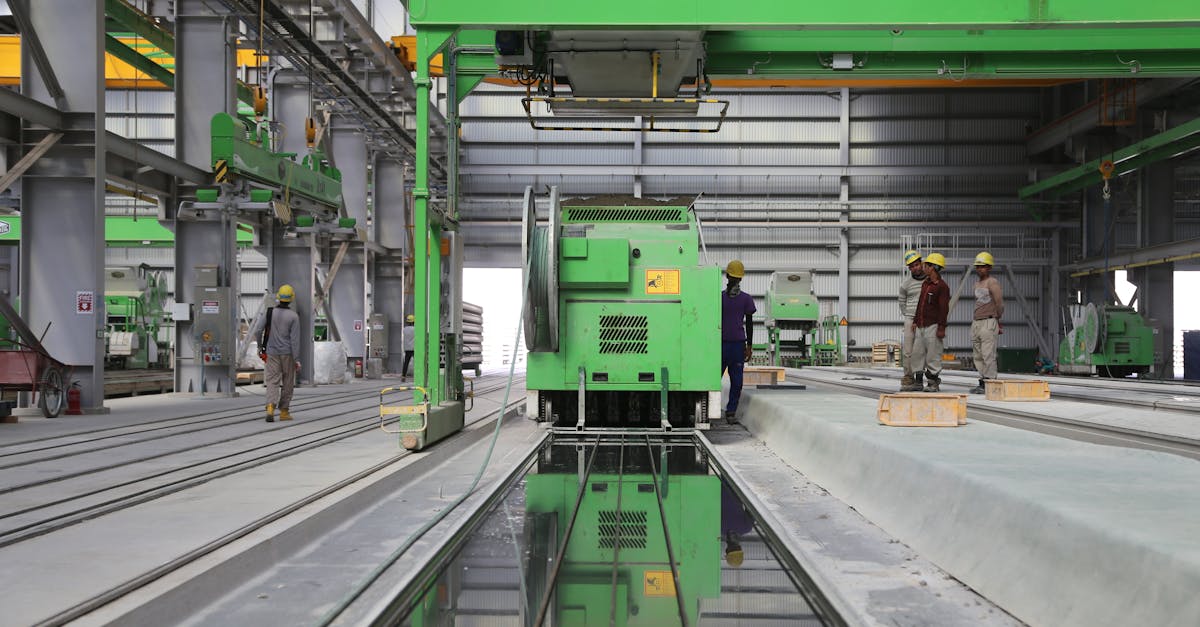
Table Of Contents
Considerations for Choosing Workholding Systems
When selecting workholding systems for CNC operations, it is essential to consider various factors to ensure optimal performance and efficiency. One critical aspect to evaluate is the type of machining operation being performed. Different workholding systems are better suited for specific processes, such as milling, turning, or drilling. Understanding the requirements of the machining operation is key to choosing the most appropriate workholding solution that can securely hold the workpiece in place.
Another important consideration is the size and shape of the workpiece being machined. Workholding systems come in a variety of configurations, such as vises, chucks, collets, and fixtures, each designed to accommodate different workpiece geometries. It is vital to select a workholding system that can effectively grip the workpiece and provide the necessary stability during machining to prevent deflection or vibration that could affect the quality of the finished part.
Factors Influencing Workholding Decisions
Factors influencing workholding decisions in CNC machining include the type of material being used, the complexity of the part, and the required precision of the final product. For example, when working with softer materials that are prone to deformation under pressure, choosing a delicate workholding system that exerts minimal force may be necessary to avoid damaging the workpiece. On the other hand, for highly intricate parts requiring extreme accuracy, a more rigid workholding setup capable of securely clamping the piece in place during high-speed machining operations may be preferred.
Furthermore, the production volume and lead time requirements can also impact workholding decisions. In high-volume manufacturing environments where efficiency is paramount, investing in quick-change workholding systems that reduce setup times can significantly increase productivity. Conversely, for low-volume production runs where setup changes are less frequent, opting for a more versatile workholding solution that can accommodate a variety of part geometries may be more practical in ensuring flexibility and cost-effectiveness.
Maintenance and Care of Workholding Equipment
Regular maintenance and care of workholding equipment is essential to ensure optimal performance and longevity. Keeping workholding devices clean from debris, coolant, and chips will help prevent contamination and damage to the equipment. Regularly inspecting for wear and tear, such as cracks or excessive wear on contact surfaces, is crucial for detecting issues early on and preventing costly breakdowns during machining operations.
Additionally, following manufacturer's guidelines for lubrication and adjusting components when necessary is important to prevent premature wear and ensure smooth operation. Proper storage of workholding equipment when not in use, avoiding exposure to harsh environmental conditions, and using protective covers or cases can also help extend the lifespan of the devices. By prioritizing maintenance and care, CNC operators can maximize the efficiency and accuracy of their machining processes while minimizing the risk of equipment failure.
Extending the Lifespan of Workholding Devices
To prolong the lifespan of custom workholding fixtures in CNC machining, it is crucial to implement a regular maintenance schedule. Keeping workholding equipment clean and free from debris is essential in preventing premature wear and damage. Regular inspection of workholding components such as clamps, vises, and fixtures can help identify any signs of wear or potential issues before they escalate into bigger problems.
Additionally, it is important to ensure that workholding devices are used within their specified load-bearing capacities. Exceeding the recommended weight limits can lead to stress on the components and result in decreased longevity. Properly securing the workpiece in the workholding system and avoiding over-tightening clamps can also help prevent unnecessary strain on the equipment. By following these maintenance practices and guidelines for usage, CNC machinists can optimize the performance and lifespan of their workholding devices.
Innovations in Workholding Technology
Innovations in workholding technology have revolutionized the way CNC machines operate. One significant advancement is the integration of smart sensors within workholding devices. These sensors can provide real-time data on clamping forces, part dimensions, and temperature, allowing for more precise and efficient machining processes. Additionally, the use of adaptive workholding systems has gained traction in the industry. These systems can automatically adjust to variations in part sizes and shapes, reducing setup times and enhancing production flexibility.
Automated Workholding Solutions in CNC
Automated workholding solutions in CNC machining have revolutionized the manufacturing industry by enhancing efficiency, precision, and productivity. These advanced systems utilize robotics and sensors to securely hold workpieces during the machining process without the need for manual intervention, thus reducing production time and improving overall quality. By integrating automation into workholding setups, manufacturers can achieve higher throughput rates and consistently accurate results, leading to cost savings and increased competitiveness in the market.
One key advantage of automated workholding solutions is the ability to optimize machining operations through continuous monitoring and adjustment of workpiece positions. The incorporation of sensors and feedback mechanisms in these systems enables real-time data collection and analysis, allowing for adaptive machining strategies and improved process control. With the capacity to make rapid modifications based on changing conditions, automated workholding solutions in CNC machining empower manufacturers to achieve greater flexibility and adaptability in their production workflows.
FAQS
What is workholding in CNC?
Workholding in CNC refers to the devices or equipment used to secure and support the workpiece during machining operations on a CNC (Computer Numerical Control) machine. It plays a crucial role in ensuring precision, accuracy, and repeatability in manufacturing processes.
Why is workholding important in CNC machining?
Workholding is essential in CNC machining as it helps in securely holding the workpiece in place, preventing movement or vibration during cutting operations. This stability is critical for achieving accurate and consistent results in production.
What are the common types of workholding systems used in CNC machining?
Common types of workholding systems in CNC machining include vises, clamps, chucks, collets, fixtures, and rotary tables. Each type is designed to accommodate different workpiece geometries and machining requirements.
How do factors like material type, workpiece size, and machining operations influence workholding decisions?
Factors such as material type, workpiece size, shape, complexity, and required machining operations play a significant role in determining the most suitable workholding solution. It is essential to consider these factors to ensure optimal performance and efficiency in CNC machining processes.
What are some tips for maintaining and caring for workholding equipment?
Regular cleaning, inspection for wear or damage, proper lubrication, and following manufacturer's guidelines for usage and maintenance are essential for prolonging the lifespan and ensuring the reliable performance of workholding equipment in CNC machining.
How can the lifespan of workholding devices be extended?
Regular maintenance, proper storage, avoiding overloading, and using workholding equipment within specified operating parameters can help extend the lifespan of workholding devices in CNC machining setups.
What are some recent innovations in workholding technology for CNC machining?
Innovations in workholding technology for CNC machining include the development of automated workholding solutions, advanced clamping systems, smart sensors for real-time monitoring, and modular workholding setups to enhance efficiency, productivity, and flexibility in manufacturing processes.
How do automated workholding solutions benefit CNC machining operations?
Automated workholding solutions in CNC machining offer advantages such as increased productivity, reduced setup times, improved accuracy, and the ability to handle complex workpiece geometries with minimal manual intervention. These advancements contribute to optimizing machining processes and enhancing overall manufacturing efficiency.